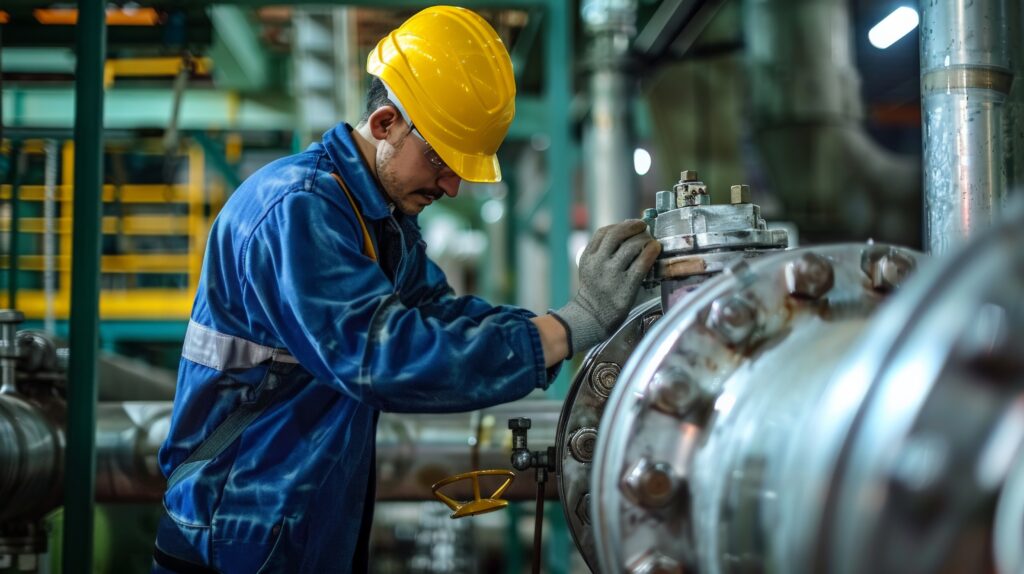
A factory worker inspecting a leak in a steel pipeline system, highlighting the importance of regular maintenance
Vacuum pumps are essential components in various industries, including manufacturing, scientific research, and even in medical applications. Ensuring that your vacuum pump operates at its peak efficiency is critical for maintaining optimal performance and extending its lifespan. While regular maintenance is necessary to keep your vacuum pump functioning smoothly, mastering advanced techniques for vacuum pump maintenance techniques can help you prevent costly repairs, improve system efficiency, and ensure a longer lifespan for the equipment.
In this blog, we will explore 10 advanced techniques for vacuum pump maintenance mastery. These tips go beyond basic maintenance tasks, delving into deeper strategies and best practices that will allow you to manage your vacuum pump like a pro, especially when working with systems like a Vacuum Furnace that require precise and reliable performance.
1. Monitor Pump Performance Using Digital Sensors
Why Digital Sensors Matter
In the past, vacuum pump performance was often assessed through traditional gauges or subjective methods. However, with advances in technology, digital sensors have become an indispensable tool for monitoring the performance of a vacuum pump. By utilizing sensors, operators can measure a range of parameters, including pressure levels, temperature fluctuations, and flow rates, providing real-time data on how well the pump is functioning.
Implementation of Digital Sensors
- Pressure Sensors: Pressure sensors can help detect even small deviations from normal operating conditions. By continuously monitoring pressure, these sensors alert you when the system is underperforming or has an issue.
- Temperature Sensors: Temperature sensors monitor the temperature of the pump’s motor and bearings. Overheating can be a sign of an impending failure, and early detection allows you to address the issue before it becomes a serious problem.
- Flow Meters: Monitoring flow ensures that the vacuum pump is operating at the optimal speed. If the flow rate drops, it might indicate clogging or a leak in the system.
Benefits
- Real-time diagnostics and troubleshooting
- Immediate alerts to prevent system failures
- Ability to track pump performance over time for trend analysis
2. Adopt Preventative Lubrication Techniques
The Role of Lubrication in Vacuum Pump Maintenance
Proper lubrication is crucial for maintaining the efficiency of your vacuum pump. Inadequate lubrication can lead to increased friction, overheating, and eventual pump failure. Beyond just refilling oil, advanced lubrication techniques focus on ensuring the right type of lubrication is applied in the right quantities at the right time, especially for specific pumps like the Single Stage Oil Sealed Vane Pump, which requires precise oil management to function optimally.
Advanced Lubrication Techniques
- Synthetic Oils vs. Conventional Oils: In high-performance applications, synthetic oils are often preferred because they provide better lubrication at higher temperatures and pressures, reducing the risk of premature wear and tear.
- Oil Changes Based on Run Time: Instead of following a fixed schedule for oil changes, track the operating hours and temperature of your pump to determine the ideal time to change the oil. Oil quality can deteriorate based on usage, so it’s essential to adjust your maintenance schedule accordingly.
- Lubrication Analysis: Periodically analyze the lubrication fluid for contaminants or degradation. A simple oil analysis can reveal internal damage or wear that is not yet visible to the naked eye.
Benefits
- Reduces wear and tear on internal components
- Prevents overheating and improves pump efficiency
- Prolongs the lifespan of the pump
3. Inspect and Clean Pump Filters Regularly
Importance of Clean Filters
Filters are responsible for removing impurities and debris from the vacuum pump’s intake and exhaust. Over time, filters can become clogged, reducing the pump’s efficiency and causing overheating. Regular filter cleaning is a key maintenance practice, but it’s the advanced techniques that will help you get the most out of your filter system.
Advanced Filter Maintenance Techniques
- Use of High-Efficiency Particulate Air (HEPA) Filters: If your application requires a high level of cleanliness, consider upgrading to HEPA filters that trap even the smallest particles.
- Backflushing Filters: Some filters can be cleaned by backflushing, which involves reversing the flow of air through the filter to remove accumulated debris. This technique is highly effective for maintaining filter performance.
- Use of Pre-Filters: In particularly dusty or dirty environments, adding a pre-filter to your system can reduce the strain on your main filter. Pre-filters catch larger particles before they reach the pump’s primary filtration system.
Benefits
- Ensures optimal airflow and pump efficiency
- Prevents clogging and overheating
- Reduces the need for expensive filter replacements
4. Inspect for Leaks with Advanced Leak Detection Methods
The Importance of Leak Detection
Leaks can drastically reduce the efficiency of your vacuum pump, causing pressure imbalances and even damaging the pump’s internal components. Simple visual inspections are not always enough to detect leaks, especially in larger systems or complex pipelines. Therefore, advanced leak detection methods are essential.
Advanced Leak Detection Techniques
- Helium Leak Detection: Helium leak detectors are sensitive to even the smallest leaks and are commonly used in critical vacuum systems. This technique involves injecting helium into the system and using a detector to trace any escaping gas.
- Vacuum Decay Testing: This method involves isolating the vacuum pump and monitoring the rate at which the pressure drops. A rapid drop indicates a leak somewhere in the system.
- Ultrasonic Leak Detection: Ultrasonic detectors can detect high-frequency sounds emitted by escaping air or gases. This method is highly effective for pinpointing small leaks in hard-to-reach areas.
Benefits
- Detects even the smallest leaks
- Ensures optimal vacuum pressure
- Prevents wasted energy and performance degradation
5. Regularly Check for Vibration and Alignment Issues
Understanding the Role of Vibration
Vacuum pumps are precision machines, and even small misalignments or excessive vibrations can cause significant wear and tear. Over time, misalignment can lead to damage to the bearings, seals, and other internal components. Detecting and correcting these issues early is essential for maintaining pump performance.
Vibration Monitoring Techniques
- Use of Vibration Sensors: Install vibration sensors to monitor the pump’s operation. Anomalies in vibration frequency or amplitude can indicate misalignment or internal damage.
- Laser Alignment Tools: Laser alignment tools allow you to precisely align the pump’s shafts, ensuring that all rotating parts are operating smoothly.
- Dynamic Balancing: If you detect vibrations, a dynamic balancing check can help identify imbalances in rotating parts, such as the impeller. Balancing the pump will reduce unnecessary wear on bearings and seals.
Benefits
- Reduces wear on pump components
- Improves pump efficiency and reliability
- Extends the lifespan of the pump
6. Maintain a Clean Environment Around the Pump
Why Environmental Cleanliness Matters
The environment surrounding your vacuum pump plays a critical role in its performance. Dust, dirt, and debris can infiltrate the system, clogging filters, and causing additional strain on the pump. Maintaining a clean environment is essential to prevent contaminants from entering the pump and damaging its components.
Advanced Environmental Maintenance Tips
- Install Protective Covers: Install covers or enclosures around your vacuum pump to prevent dust and debris from entering.
- Air Filtration Systems: Use air filtration systems to purify the air in the pump room. Clean air reduces the risk of contamination, helping maintain the pump’s efficiency.
- Floor Maintenance: Keep the floor around the pump clean by frequently sweeping or vacuuming. The buildup of dust on the floor can easily make its way into the system.
Benefits
- Reduces the risk of contamination and clogging
- Improves system reliability and performance
- Minimizes the frequency of filter changes and repairs
7. Perform Regular Seal Inspections and Replacements
Importance of Seals in Vacuum Pumps
Seals are one of the most important components in maintaining the integrity of a vacuum pump. A damaged or worn seal can cause leaks, reducing the efficiency of the pump and leading to further damage. Regular seal inspections and replacements are necessary to prevent these issues.
Seal Maintenance Techniques
- Visual Inspections: Regularly check the seals for signs of wear or cracking. Look for any visible leaks around the pump’s seals or flanges.
- Seal Lubrication: Some seals benefit from periodic lubrication to reduce friction and wear. Follow the manufacturer’s recommendations for the appropriate type of lubricant.
- Seal Material Upgrades: If your pump is subject to extreme temperatures or chemicals, consider upgrading to seals made from more durable materials like Viton or PTFE.
Benefits
- Prevents leaks and loss of vacuum pressure
- Improves overall system efficiency
- Reduces maintenance costs in the long run
8. Regularly Test and Calibrate Vacuum Gauges
Why Calibrating Gauges Is Crucial
Vacuum gauges provide essential feedback about the pump’s performance. However, over time, gauges can lose accuracy, leading to incorrect readings. Regularly testing and calibrating your vacuum gauges is necessary to ensure that the readings are reliable and accurate.
Gauge Maintenance Techniques
- Regular Calibration: Calibration should be performed at least once every six months, depending on the pump’s usage. Use a calibrated reference gauge to ensure accuracy.
- Check for Drift: Monitor the gauge’s performance over time. If the readings start to drift, it may indicate an issue with the gauge that needs to be addressed.
- Gauge Cleaning: Clean the gauges periodically to remove any dirt or grime that may interfere with accurate readings.
Benefits
- Ensures accurate performance monitoring
- Helps in early detection of potential issues
- Improves overall system reliability
9. Implement a Vacuum Pump Monitoring System
Understanding Vacuum Monitoring Systems
In larger or more complex systems, manually monitoring a vacuum pump can be cumbersome. Implementing an integrated vacuum pump monitoring system allows for continuous data collection, analysis, and remote monitoring of your pump’s performance.
Features of Advanced Monitoring Systems
- Remote Monitoring: Allows technicians to monitor the pump’s performance from a central location, reducing downtime and troubleshooting time.
- Predictive Maintenance: Advanced systems can predict potential failures by analyzing performance data and providing early warnings.
- Data Logging: Continuous data logging ensures that you have a detailed record of your pump’s performance, which is valuable for troubleshooting and optimization.
Benefits
- Streamlines maintenance processes
- Provides data for performance optimization
- Allows for proactive maintenance and reduced downtime
10. Train Operators and Technicians on Advanced Maintenance Practices
The Importance of Operator Training
Even the best maintenance strategies are ineffective if operators and technicians are not properly trained. Providing your team with advanced training on vacuum pump maintenance ensures that they can identify issues early, perform necessary repairs, and implement preventive measures effectively.
Training Program Recommendations
- Regular Workshops: Conduct regular training workshops to keep operators updated on the latest maintenance techniques and technologies.
- Hands-On Experience: Ensure technicians gain hands-on experience with the equipment, allowing them to identify potential issues and perform routine maintenance tasks with confidence.
- Safety Protocols: Train operators on safety procedures to avoid accidents during maintenance tasks, especially when dealing with high-pressure or high-temperature systems.
Benefits
- Increases team competence and confidence
- Reduces the risk of human error
- Ensures optimal pump performance through skilled operation
Conclusion
Mastering vacuum pump maintenance involves more than just routine checks and oil changes. By implementing advanced techniques such as digital monitoring, precise lubrication practices, and sophisticated leak detection, you can maximize your pump’s efficiency, reduce downtime, and extend its lifespan. Whether you’re running a small laboratory or a large industrial operation, these 10 advanced techniques will help you achieve vacuum pump maintenance mastery and keep your system running smoothly for years to come.
Also Read: Top Productivity Tools to Boost Your Efficiency and Focus