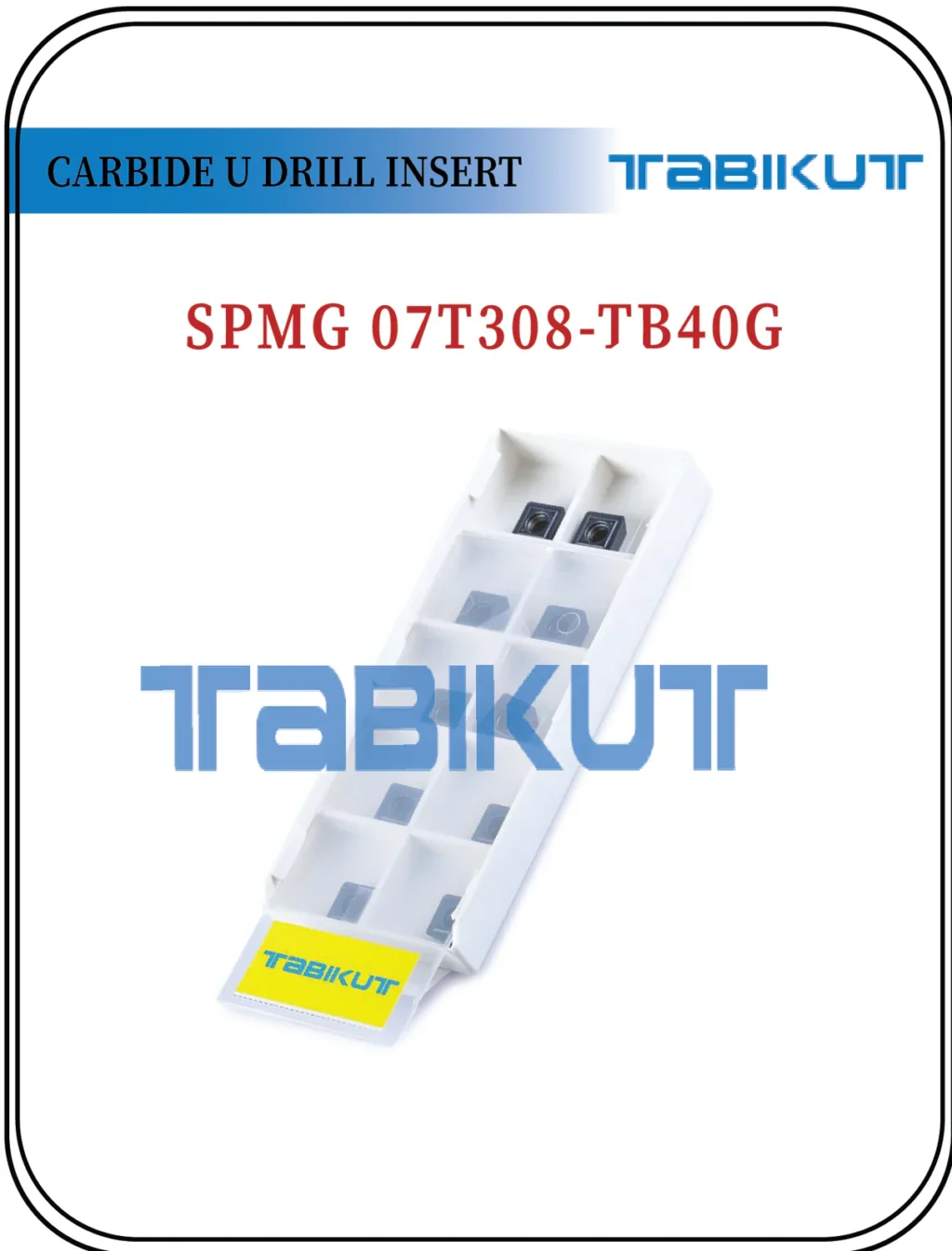
Introduction
In modern machining drilling inserts are commonly used to improve efficiency and precision. The efficiency of the drilling process has been greatly improved by their modern design and composition of the material.
What Is a Drilling Insert?
An drilling insert is defined as a consumable cutting instrument that’s attached to an existing drill body. Instead of repeatedly sharpening tools inserts are made to be repaired when used, which makes them highly efficient for industrial applications.
How Drilling Inserts Work
Material Removal Process
During the operation the material is removed as the insert is pushed against the workpiece. The cutting edges are designed to withstand high-speed movements as well as extreme temperatures, which allows the formation of holes to be consistent.
Compatibility With Machines
Drilling inserts are typically used on CNC machines as well as other systems that are automated. Different types of geometries and coatings are picked depending on the needs of the application and the material type being the drills.
Benefits Offered by Drilling Inserts
Reduced Downtime
Since the insert can be easily changed, tool changes are decreased. In the end, productivity is improved without damaging the quality.
Consistent Surface Finish
Precision-ground inserts are used to ensure uniformity across different workpieces. Even in the most difficult conditions, the surface finishes are maintained.
Cost Efficiency
Instead of replacing the entire tool in the process, only inserts are changed. In time, substantial cost savings can be made particularly in high-volume operations.
Types of Drilling Inserts
By Shape
- Triangular inserts are used for general-purpose drilling.
- Round inserts are selected for their higher feed rates and longer cuts.
By Application
- Inserts that can be indexable are typically used when drilling deep holes.
- Solid inserts are reserved for certain alloy cutting.
Factors to Consider When Choosing a Drilling Insert
Coating and Material
Different coatings like TiAlN or CVD are favored according to their wear resistance and temperature. Carbide inserts are widely used due to their long-lasting properties.
Workpiece Material
The geometry of the insert must be compatible with the material of the workpiece. For example, stainless steel has different specifications when compared to cast iron or aluminum.
Maintenance and Replacement Tips
- Inserts should be inspected visually at the end of each use.
- It is recommended to follow the torque settings when installing.
- Edges that are chipped or dull should be replaced immediately in order to avoid damaging the workpiece.
Conclusion
The importance of inserts for drilling in the modern machine should not be ignored. By incorporation of them into manufacturing processes, improved performance and longer life of the tool are guaranteed. Continuous advances in the field of insert design and material science could improve the drilling process across different industries.