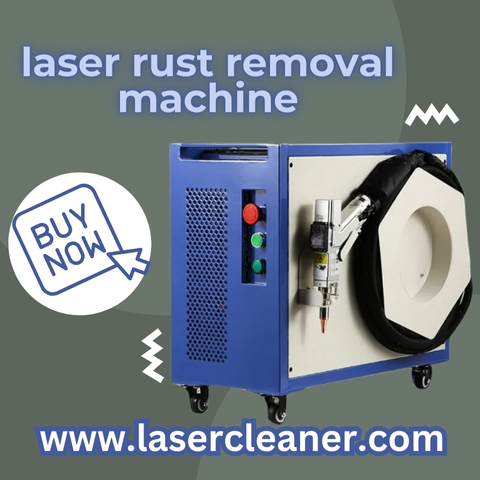
Rust is the relentless enemy of metal, silently consuming surfaces, weakening structures, and destroying aesthetics. For industries, workshops, and restoration projects, tackling rust efficiently is critical. While traditional methods like sandblasting, chemical treatments, and grinding have been widely used, they often fall short in terms of precision, safety, and surface integrity. Enter the laser rust removal machine—a groundbreaking approach reshaping the way we eliminate corrosion.
This in-depth guide explores how a laser rust removal machine works, where it’s used, why it’s making waves in various industries, and what to consider when adopting this technology.
What Is a Laser Rust Removal Machine?
A laser rust removal machine is an advanced cleaning device that uses laser beam technology to remove rust, oxidation, paint, and other surface contaminants from metals and certain non-metal surfaces. Rather than scraping or dissolving the corrosion physically or chemically, the laser interacts with the rust layer through a process called laser ablation. This high-energy beam breaks down and vaporizes rust without touching the metal underneath.
The core idea is simple yet powerful: rust and base metal absorb laser energy differently. The machine is calibrated to deliver energy at a level that the rust absorbs while the metal reflects. This selective targeting allows for precise rust removal while preserving the structural integrity and aesthetics of the material.
The Science Behind Laser Rust Removal
Laser ablation is the scientific principle at work here. The laser rust removal machine emits short pulses of high-energy light. When this energy hits the rust (usually iron oxide), it heats it rapidly, causing it to either sublimate (go directly from solid to gas) or break down into particles that can be vacuumed or blown away. Since the base metal has a higher thermal conductivity and reflectivity, it absorbs much less energy, remaining unaffected.
Moreover, modern machines are equipped with real-time sensors and adjustable parameters. This ensures that the energy delivered is customized to the type and thickness of the rust, minimizing risks and improving efficiency.
Industrial Applications and Use Cases
A laser rust removal machine isn’t just a high-tech gadget; it’s becoming a critical tool across multiple industries:
1. Manufacturing and Fabrication
Factories use these machines to clean parts before welding, painting, or coating. Clean metal surfaces improve adhesion, reduce defects, and enhance product longevity.
2. Automotive and Transportation
From restoring vintage cars to maintaining railway components and aircraft parts, removing rust is essential. A laser rust removal machine ensures thorough cleaning without damaging valuable parts or requiring dismantling.
3. Marine and Shipbuilding
Saltwater exposure leads to aggressive rusting. Ships, submarines, and offshore structures require constant maintenance. Laser rust removal provides a cleaner, drier, and environmentally safer solution than abrasive blasting.
4. Oil and Gas
Pipelines, rigs, and storage tanks suffer from constant exposure to moisture and chemicals. Quick, non-destructive rust removal is essential for safety and compliance.
5. Military and Defense
Tank armor, firearms, and other equipment need precision cleaning. A laser rust removal machine allows for targeted surface prep and restoration without affecting coatings or structural properties.
Safety and Environmental Considerations
Unlike traditional methods that generate toxic waste or involve chemical exposure, the laser-based approach is significantly cleaner. Rust and paint are turned into harmless dust or gas and captured by filters, reducing health hazards for workers and environmental contamination.
However, using a laser rust removal machine still requires proper safety measures:
-
Eye Protection: Operators must wear laser safety goggles to prevent retinal damage.
-
Ventilation: The vaporized material may include harmful particulates, so ventilation or vacuum systems are vital.
-
Training: Understanding how to handle the machine, adjust settings, and target the surface correctly ensures both safety and optimal performance.
Factors to Consider Before Buying
If you’re considering adding a laser rust removal machine to your workspace, here are some critical factors to keep in mind:
Power Rating
Laser power (typically from 20W to over 2000W) affects the depth and speed of cleaning. High-powered units are suitable for industrial-scale tasks, while lower-powered machines are ideal for light-duty or precision work.
Portability
Some models are handheld and compact, ideal for fieldwork or mobile workshops. Others are larger, stationary systems designed for high-volume or automated tasks.
Material Compatibility
While laser rust removal works well on metals, it’s not suitable for every surface. Understanding your material types ensures better results.
Surface Area and Depth
Machines vary in their ability to clean large surfaces or reach into narrow spaces. The spot size, beam type (pulsed or continuous), and scanning system determine this capability.
Budget and Maintenance
Though the upfront cost may be higher than sandblasting gear, maintenance is lower, and there’s no need for consumables like sand or chemicals.
Comparing with Traditional Rust Removal Methods
To understand the value of a laser rust removal machine, it’s helpful to contrast it with legacy methods:
-
Sandblasting: Effective but messy, noisy, and damaging to the substrate.
-
Chemical Cleaners: Require disposal systems and pose health risks.
-
Manual Grinding: Labor-intensive and lacks precision.
-
Electrolytic Cleaning: Suitable only for small or removable parts.
Laser cleaning stands out by offering precise, contactless, and repeatable results without the logistical drawbacks of conventional methods.
Future Trends and Technological Evolution
Laser cleaning is still evolving. As demand grows, machines are becoming more affordable, compact, and intelligent. Integration with robotics and AI-driven sensors (for automation and surface recognition) is on the rise in large-scale industrial settings. Research is also focused on multi-material compatibility and energy efficiency to broaden the application scope.
The rise of green technologies further amplifies the appeal of a laser rust removal machine, particularly for industries looking to minimize their carbon footprint and reduce operational hazards.
Maintenance Tips for Long-Term Use
Owning a laser rust removal machine is an investment that requires proper care:
-
Clean Optics Regularly: Dust or residue on the lens can distort the beam and reduce effectiveness.
-
Check Cooling Systems: Some high-powered models include water or air cooling. Ensure it’s functioning properly.
-
Update Firmware: If your machine includes digital controls, keeping firmware updated helps maintain efficiency.
-
Store Properly: Protect the device from moisture, dust, and extreme temperatures when not in use.
-
Operator Training: Ensure all users are trained not just in operation but also in routine troubleshooting.
Final Thoughts
A laser rust removal machine represents more than just a rust-cleaning tool—it’s a transformative piece of technology that is changing the face of industrial surface maintenance. From automotive restoration to aerospace maintenance, this machine delivers unmatched precision, cleanliness, and control.
Whether you’re a small workshop looking to modernize your restoration services or an industrial giant maintaining massive infrastructure, incorporating this technology can streamline your processes, reduce waste, and raise your operational standards.