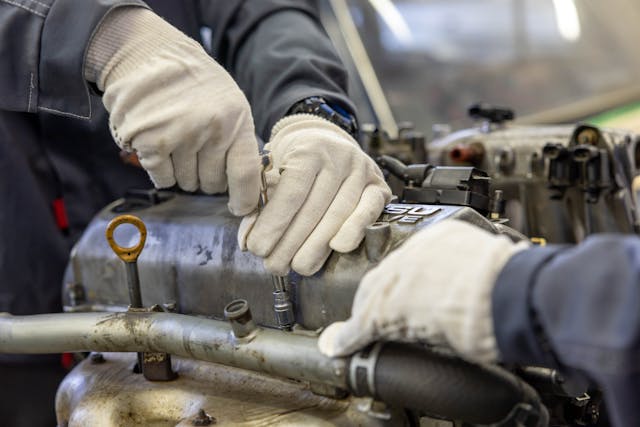
In the heart of Oklahoma, many businesses rely on electric motors to drive their operations, from manufacturing plants to agricultural facilities. These motors are essential for powering machinery, ensuring that processes run smoothly. However, when an electric motor fails, the consequences can be significant. Understanding the costs associated with downtime and the importance of prompt electric motor repair and service can help businesses mitigate losses and maintain operational efficiency.
The Hidden Costs of Downtime
When an electric motor fails, the immediate reaction is often to address the problem. However, the costs associated with downtime extend far beyond the repairs themselves. Here are some key factors to consider:
1. Lost Revenue
One of the most immediate impacts of motor failure is the loss of revenue. Every minute a production line is halted or machinery is idle translates to lost income. In manufacturing, this could mean not meeting orders, resulting in dissatisfied customers and potential loss of future business.
2. Increased Labor Costs
During downtime, labor costs can increase as employees are left waiting for machines to be repaired. This wasted time can lead to frustration among staff and a decline in morale. Additionally, if overtime is required to catch up on lost production, costs can escalate further.
3. Supply Chain Disruptions
For many businesses, electric motors play a key role in supply chain management. A failure can disrupt not just internal operations but also affect suppliers and customers. Delays in production can ripple through the supply chain, causing delays in deliveries and impacting relationships with vendors and customers.
4. Equipment Wear and Tear
When a motor fails, other connected machinery may also suffer. For example, if a conveyor system is halted suddenly, it can cause additional stress on gears and bearings. This wear can lead to further repair costs and more extended downtime down the road.
5. Safety Risks
Motor failures can pose safety risks to employees. A sudden stop can lead to accidents, injuries, or unsafe working conditions. Ensuring that motors are in good working order not only protects machinery but also safeguards the well-being of employees.
The Importance of Swift Electric Motor Repair and Service
Given the potential costs associated with downtime, it’s crucial for businesses to prioritize swift electric motor repair and service. Here’s why prompt action is essential:
1. Minimizing Downtime
The faster a motor can be repaired, the less downtime a business will experience. Quick response times can significantly reduce the financial impact of a failure. Having a reliable repair service on speed dial can make all the difference when a motor issue arises.
2. Preventing Larger Issues
Addressing problems early can prevent more significant issues from developing. For example, catching a minor electrical fault before it leads to a complete motor failure can save time and money. Regular maintenance and swift repairs can extend the lifespan of motors and ensure they operate efficiently.
3. Enhancing Operational Efficiency
When motors are functioning properly, businesses can operate at peak efficiency. This efficiency translates to higher productivity and better quality products. Swift repairs help maintain that efficiency, allowing companies to meet production goals and customer demands.
4. Strengthening Safety Protocols
Regular maintenance and prompt repairs contribute to a safer working environment. Ensuring that motors are in good condition helps prevent accidents and keeps employees safe. Companies that prioritize safety often see improved employee morale and decreased turnover rates.
5. Building Customer Trust
Reliability is key in any business relationship. By minimizing downtime and maintaining consistent production schedules, companies can build trust with their customers. This reliability can lead to repeat business and positive referrals.
Strategies for Mitigating Downtime
To effectively manage the risks associated with motor failure, Oklahoma businesses can implement several strategies:
1. Regular Maintenance Programs
Establishing a routine maintenance program is essential for identifying potential issues before they escalate. Regular inspections, lubrication, and performance assessments can help keep electric motors in optimal condition.
2. Staff Training
Investing in employee training can empower staff to recognize early signs of motor distress. By equipping employees with the knowledge to identify potential issues, businesses can take proactive measures to address problems before they lead to failure.
3. Utilize Technology
Implementing technology, such as predictive maintenance software, can provide valuable insights into motor performance. Monitoring tools can help track vibrations, temperatures, and other critical metrics, allowing for early intervention when abnormalities are detected.
4. Build Relationships with Repair Services
Having a reliable electric motor repair and service provider is crucial. Establishing a relationship with a reputable service can ensure quick response times and expert assistance when issues arise. This partnership can help reduce downtime and facilitate efficient repairs.
5. Maintain Inventory of Spare Parts
Keeping an inventory of critical spare parts can significantly reduce repair times. If a motor requires a specific component, having it on hand can expedite the repair process and minimize downtime.
Case Studies: The Impact of Swift Repair
To illustrate the benefits of prompt electric motor repair and service, consider the following case studies from Oklahoma businesses:
Manufacturing Plant
A manufacturing plant experienced a sudden motor failure on a key production line. The plant had a maintenance program in place, which allowed them to identify the issue early. They quickly contacted their electric motor repair service, and technicians were on-site within hours. The motor was repaired promptly, resulting in only minimal downtime. The plant was able to meet its production goals and maintain customer satisfaction.
Agricultural Facility
In an agricultural facility, a motor responsible for irrigation systems failed during a critical growing season. The facility had established a relationship with a local repair service. As soon as the problem was reported, technicians were dispatched immediately. Their swift response minimized the impact on crop yields, demonstrating the value of having reliable repair services on hand.
HVAC Company
An HVAC company relied on electric motors for its cooling systems. When a motor failure occurred during peak summer months, the company faced the risk of losing customers. They quickly engaged their electric motor repair service, which provided rapid support. The motor was repaired, and the company was able to maintain its service contracts and customer trust.
Conclusion
The ripple effect of electric motor failure can have significant consequences for businesses in Oklahoma. Understanding the costs associated with downtime and the importance of swift electric motor repair and service can help companies mitigate these risks. By prioritizing maintenance, investing in training, and building relationships with reliable service providers, businesses can ensure their electric motors operate efficiently and effectively.
In a competitive landscape, minimizing downtime and maintaining operational efficiency is crucial for success. By taking proactive measures and responding quickly to motor issues, Oklahoma businesses can navigate the challenges of electric motor failures and emerge stronger and more resilient.