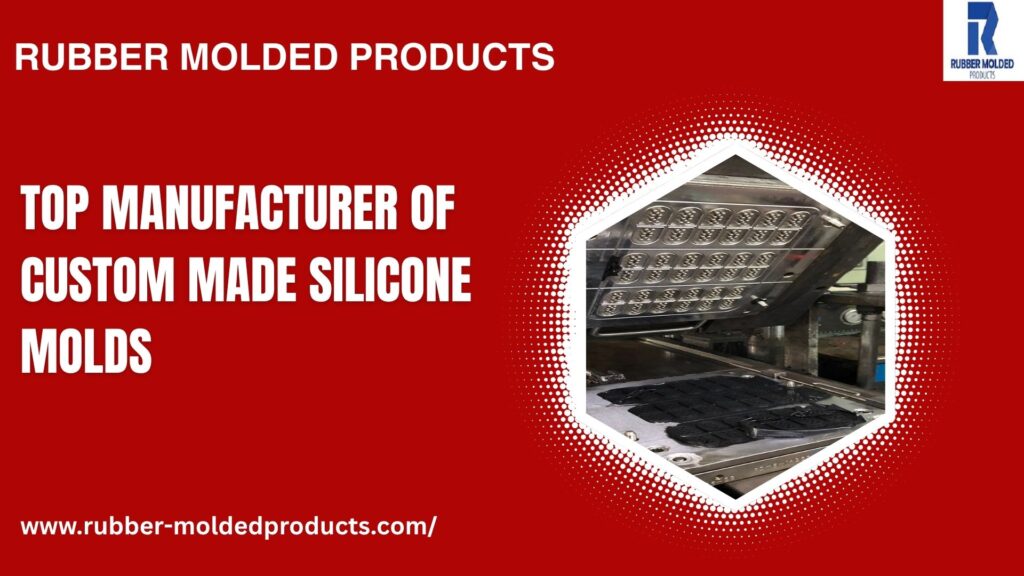
Custom made silicone molds are employed to produce precise and high-performance silicone parts. They work with industries where precision, toughness, and elasticity is needed. They become important in manufacturing parts which fit perfectly and have a longer lifespan.
The top manufacturers use the latest molding techniques to achieve specific product requirements. They balance technical acumen with practical know-how in delivering improved results. The process helps brands save time and prevent expensive production errors.
Silicone molds require high levels of quality in their strength and performance. The teams use top-grade materials and accurate tooling. Such molds apply throughout medical, electronics, food, and consumer goods industries. They guarantee every part operates safely and uniformly under stress.
Many rubber parts manufacturers also provide design assistance and material recommendation guidance. This enables clients to prevent errors and improve product efficiency. A trusted producer constructs molds that facilitate innovation and business development. They collaborate with customers from design to delivery without any delays.
Some Qualities of a Top Custom Silicone Mold Manufacturer
A custom silicone mold manufacturer provides more than generic molds. They need to provide custom solutions for sectors such as medical, food, and electronics. The project starts with a clear understanding of the end-use requirements of the client. They need to be flexible enough to change according to the part shape or purpose.
High-accuracy different molding methods are used by the best manufacturers.
- Injection molding is suitable for high-volume as well as intricate part production.
- Compression molding works perfectly when there is a need for large and uncomplicated parts.
- Transfer molding is perfect for parts with inserts or inculcated elements.
Rapid prototyping is important for launching new products. The manufacturers have to make rapid samples for trials or modifications. They should provide sample components without a high price tag. This helps brands in minimising risks and gauging the market effectively.
The teams need to have skills to deal with intricate shapes and high-angle designs. A custom silicone molding has to handle intricate channels, threads, or undercuts. They should ensure strict specs in each production run.
These distinguish good makers from reliable industry leaders. The right partner is about better performance, faster results, and enduring value. Many manufacturers offer complete support from creation to delivery with no shortcuts. They stay agile, responsive, and innovation-driven, not expedient.
Advanced Silicone Molding Techniques
Any buyers ask for advanced silicone molding process. This is the most important factor in making high-performance and long-lasting parts. The appropriate method varies according to the product design, volume, and purpose. The top rubber molding companies use certain procedures as per industry requirements and material necessities.
Liquid Injection Molding
This method is best suited for close tolerances and repetitive quality. Liquid silicone is pressed into a mold at high speed and pressure. It’s ideal for production in bulk with repeat results and low waste. The medical and electronics sectors use this process.
Compression Molding
Compression molding is an excellent option for simpler and more effective silicone parts. A pre-measured piece of silicone is loaded into a hot mold. The material forms a shape as the mold closes under pressure. It is ideal for low-cost and low-volume production.
Transfer Molding
This process facilitates accurate detail and even surface finishes. Silicone is forced through a runner into the mold cavity. This is particularly good for parts with inserts or intricate geometries.
Why Material Choices Matter?
The most quality rubber parts manufacturers produce with platinum-cured and high-strength silicone rubbers. These provide improved durability and biocompatibility. They are resistant to heat, chemicals, and stress-tearing. These are suitable for harsh or sensitive environments.
Industry Applications
Custom made silicone molds are used in various industries. The industries have some requirements based on safety, performance, and durability. The flexibility and strength of the silicone make it best suited for hostile environments. The manufacturers make parts based on strict industry regulations.
Medical Industry
Medical silicone is used on tubes, seals, and surgical equipment. It must be safe, non-reactive, and chemical and heat resistant. Companies ensure that these parts meet regulations and patient safety requirements.
Automotive and Electronics
Silicone parts are resistant to heat, vibration, and exposure to liquids. Seal, gasket, and interior trim are some automobile uses. Silicone insulates and protects from moisture and dust in electronics. The consistency of the material rules out failure in high-risk uses.
Prototyping and Testing
A custom manufacturer of silicone molds facilitates product development from concept to marketplace. They offer molds for quick prototyping, testing, and low-volume manufacturing. These activities are vital to detect defects and optimize design early.
Silicone molding ensures brands in a variety of industries perform on tight deadlines and performance criteria.
Why Choose Rubber-MoldedProducts Company for Custom Silicone Molds?
Rubber-MoldedProducts is a reputable firm for accurate, high-quality silicone mold solutions. They identify what various industries require. Their team provides repeated consistency and meets even the most challenging requirements. You receive parts that fit, last, and perform every time.
They use special machines and techniques for custom silicone molding. This guarantees that the molds pick up details and tight tolerances. They accommodate several types of molding, such as injection, compression, and transfer.
Rubber-MoldedProducts prides itself on quick turnaround of custom orders. They can handle urgent prototypes without sacrificing accuracy. The speed advantage enables brands to compress product development timelines and conduct ideas more quickly.
They also offer full-service assistance through each phase of production. You get updates, design comments, and sincere suggestions on time. They assist you even after the completed product is handed over to you.
What sets them apart from other rubber molding companies is dependability. They enforce rigorous quality control for all the processes and batches of production. You receive experienced guidance, fast implementation, and proven products.
Conclusion
An expert team provides parts that are precise fit, form, and function. They know design requirements and use the optimal process for each job. You save time, eliminate rework, and receive consistent quality every time.
They pair expertise with new technology and materials. They quickly respond to shifts in demand, design, or volume. The technical support will result in fewer mistakes and more efficient production cycles.
The custom made silicone molds save waste, enhance performance, and provide long-term value. The highest quality molding companies provide more than mere manufacturing. They become trusted partners from the idea to delivery.
Make your ideas a reality with custom silicone molds from industry leaders. Get advanced technology, quick turnaround, and expert guidance every step of the way. Reach out to us today to talk about your project and enjoy precision, durability, and quality.