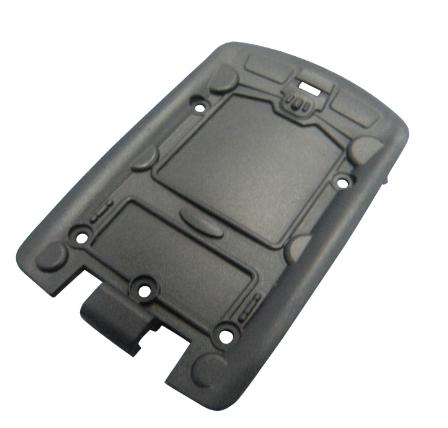
Innovations in Injection Molding: A Comprehensive Guide
Injection molding is a vital process in the manufacturing sector, enabling the production of high-quality plastic parts efficiently. As industries evolve, so does injection molding, driven by technological advancements and the need for sustainable practices. This article explores the latest innovations, market trends, and challenges in the injection molding industry. For more insights on China injection molds and the importance of injection molding near me, explore our resources.
What is Injection Molding?
Injection molding is a manufacturing process that involves injecting molten material into a mold to create specific shapes. It is widely used for producing plastic components in various sectors, including automotive, consumer goods, and medical devices. The process offers numerous advantages, such as:
- High Efficiency: Injection molding can produce large quantities of parts quickly, making it ideal for mass production.
- Complex Shapes: The technique allows for intricate designs that would be difficult or impossible to achieve with other methods.
- Material Versatility: A wide range of materials can be used, including thermoplastics and thermosetting plastics.
Key Innovations Transforming the Industry
Recent years have seen significant innovations in injection molding technology. Here are some key developments:
1. Advanced Materials
The introduction of new materials has revolutionized injection molding. Manufacturers are now exploring:
- Biodegradable Plastics: These materials break down naturally, reducing environmental impact and catering to eco-conscious consumers.
- High-Performance Polymers: These offer enhanced durability and resistance to heat, making them suitable for demanding applications.
2. Automation and Robotics
Automation is becoming increasingly prevalent in injection molding. Benefits include:
- Increased Precision: Automated systems enhance accuracy, reducing defects in production.
- Cost Efficiency: By minimizing labor costs and maximizing output, automation leads to significant savings.
3. Smart Manufacturing
The integration of Industry 4.0 technologies is transforming injection molding. This includes:
- IoT Connectivity: Machines can communicate and share data, allowing for real-time monitoring and adjustments.
- Predictive Maintenance: Data analytics predict when maintenance is needed, reducing downtime and improving efficiency.
Sustainability in Injection Molding
Sustainability is a growing concern in the manufacturing sector. The injection molding industry is making strides to reduce its environmental footprint through various initiatives:
1. Energy Efficiency
Manufacturers are investing in energy-efficient machines that consume less power during production. This not only lowers operational costs but also contributes to a greener manufacturing process.
2. Recycling Initiatives
Many companies are adopting practices to recycle scrap materials generated during production. By reusing these materials, manufacturers can significantly reduce waste and support a circular economy.
3. Sustainable Sourcing
Sourcing materials from sustainable suppliers is becoming a priority. This ensures that the raw materials used in injection molding processes have a minimal environmental impact.
Market Trends Influencing Injection Molding
Several market trends are shaping the future of injection molding:
1. Demand for Customization
Consumers increasingly seek personalized products. Injection molding allows for customization without significantly increasing production costs, making it a popular choice in various industries.
2. Growth of the Medical Sector
The medical industry is expanding rapidly, leading to increased demand for specialized injection molded components. Manufacturers focus on producing high-quality, sterile products that meet stringent regulatory standards.
3. Rise of Electric Vehicles
With the automotive industry shifting towards electric vehicles, there is a growing need for lightweight and durable plastic components. Injection molding is well-suited to meet these demands.
Challenges Facing the Injection Molding Industry
Despite its advancements, the injection molding industry faces several challenges:
1. Rising Material Costs
The cost of raw materials, particularly plastics, is on the rise. This can impact profit margins for manufacturers, prompting them to explore alternative materials and optimize their supply chains.
2. Skilled Labor Shortage
As technology advances, there is a growing need for skilled labor to operate sophisticated machinery. The industry must invest in training programs to equip workers with the necessary skills.
3. Environmental Regulations
Increasingly stringent environmental regulations require manufacturers to adopt sustainable practices, which can be challenging and costly to implement.
The Role of AI in Injection Molding
Artificial intelligence is beginning to play a crucial role in the injection molding industry. AI can analyze production data to identify patterns and optimize processes. This leads to improved efficiency, reduced downtime, and enhanced product quality.
Conclusion: Embracing Change in Injection Molding
The future of injection molding is bright, characterized by innovation and a commitment to sustainability. As manufacturers embrace new technologies and adapt to changing market demands, the industry will continue to thrive. By focusing on efficiency, quality, and environmental responsibility, injection molding will remain a vital part of the manufacturing landscape.
Table: Key Innovations in Injection Molding
Innovation | Description | Impact |
---|---|---|
Advanced Materials | Development of biodegradable plastics | Reduces environmental impact |
Automation | Integration of robotics in production | Increases efficiency and precision |
Smart Manufacturing | Use of IoT for data collection | Optimizes production processes |
Energy Efficiency | Investment in energy-efficient machines | Lowers operational costs |
Recycling | Practices to recycle scrap materials | Contributes to a circular economy |