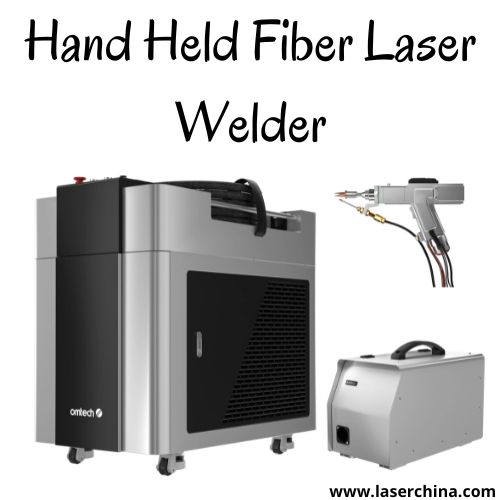
In the evolving world of metal fabrication and repair, technologies continue to advance at an impressive pace, pushing the boundaries of what was once thought possible. Among these breakthroughs, the hand held fiber laser welder stands out as a revolutionary tool, reshaping the way professionals approach welding tasks across multiple industries.
To address the question—can a hand held fiber laser welder truly replace traditional welding methods in every metal repair job?—we must take a deep dive into what this technology is capable of, how it functions, and why it has become increasingly popular. Understanding these elements reveals why this device is not just a replacement but a significant evolution in welding technology.
What Is a Hand Held Fiber Laser Welder?
A hand held fiber laser welder is a portable welding device that uses a focused fiber laser beam to join metal surfaces. Unlike traditional welding, which relies on heat generated by electric arcs or gas flames, fiber laser welding harnesses a highly concentrated light beam to melt and fuse metals with precision and speed.
This portability factor, combined with the power of fiber laser technology, enables users to weld difficult-to-reach areas, perform repairs on-site, and work with a variety of metals with minimal preparation. The laser’s intensity melts the metal surfaces instantly, creating a clean and strong weld.
Why Is It Gaining Traction?
One of the reasons the hand held fiber laser welder is gaining traction in metalworking environments is its unmatched precision. The laser beam can be controlled with great accuracy, allowing welders to create tight, seamless joins without excessive heat distortion. This precision reduces the risk of weakening the surrounding material, a common challenge in traditional welding methods.
Moreover, the speed of welding is significantly faster. Laser welding can complete tasks in seconds that might take much longer with conventional methods. This efficiency can translate into higher productivity and lower labor costs, an enticing prospect for professionals who manage high-volume repair or fabrication work.
Versatility in Applications
The hand held fiber laser welder has found uses across automotive repairs, aerospace maintenance, jewelry crafting, and heavy machinery upkeep. This versatility arises because the device can handle different types of metals including steel, aluminum, copper, and even exotic alloys, adapting easily to the demands of various industries.
Another critical factor is its minimal preparation requirement. Unlike traditional welding, which often demands extensive cleaning, grinding, or setup, fiber laser welding can often be performed on surfaces with less preparation. This reduces downtime and enhances workflow, especially in repair scenarios where time is critical.
Portability and Accessibility
The design of the hand held fiber laser welder offers portability, which has never been a feature of traditional welding rigs. This means users can bring the welder directly to the workpiece, rather than transporting large parts to a fixed welding station. This flexibility is invaluable in field repairs or tight spaces where conventional equipment cannot easily fit.
The ergonomic design also reduces fatigue for the operator. With controls integrated into the handheld unit, welders can work more comfortably and with greater control. This reduces the risk of errors and improves the overall quality of the welds produced.
Quality of Welds
Fiber laser welding produces welds that are often cleaner and require less post-processing. Because the heat-affected zone is narrow, the risk of warping or cracking is minimized. This characteristic is particularly important in applications where precision and structural integrity are paramount, such as aerospace or medical device manufacturing.
Additionally, the welds made by a fiber laser are typically visually superior, with smooth, shiny finishes that often eliminate the need for grinding or polishing. This not only saves time but also enhances the aesthetic appeal of the finished product.
Environmental and Safety Considerations
Fiber laser welding technology is also known for being more environmentally friendly compared to traditional welding. It does not require the use of shielding gases or consumable electrodes, which reduces waste and the potential release of harmful substances. Additionally, the localized heat application minimizes energy consumption and reduces the overall carbon footprint of the welding process.
From a safety perspective, although all welding requires protective gear, the hand held fiber laser welder reduces exposure to fumes and spatter, common hazards in conventional welding. This improvement contributes to a safer working environment and less need for extensive ventilation systems.
Challenges and Adaptations
While the hand held fiber laser welder is incredibly versatile, it is important to recognize that certain very thick materials or specific welding applications might still require traditional methods or specialized laser equipment. However, as technology continues to advance, these limitations are becoming less pronounced.
Operators using hand held fiber laser welders must also be trained to handle the specific characteristics of laser welding. The precision and power of the laser beam require skill and understanding to optimize weld quality and ensure safety.
Why Should Professionals Consider a Hand Held Fiber Laser Welder?
For metalworkers, repair technicians, and fabricators looking to modernize their toolkit, the hand held fiber laser welder offers an exciting opportunity. It streamlines workflows by reducing setup times, welding faster with higher precision, and allowing greater flexibility in challenging environments.
Its ability to weld on-site without the constraints of bulky equipment is a game-changer. Repairs that once meant costly transportation or disassembly can now be done quickly and efficiently. For businesses, this translates into cost savings, faster turnaround times, and improved customer satisfaction.
Furthermore, the durability and quality of welds produced by fiber laser technology can enhance the lifespan and performance of repaired parts, reducing future maintenance needs.
Market Trend and Future Outlook
The market for portable fiber laser welders is expanding rapidly as more industries recognize the advantages of this technology. Innovations continue to push the limits on power output, size reduction, and ease of use, making these devices more accessible to small businesses and individual professionals.
The future will likely see even greater integration of fiber laser welders with automation and smart controls, enabling even higher consistency and quality in welding processes. For anyone involved in metal joining, staying ahead means embracing such innovations early.
Final Thoughts
A hand held fiber laser welder is far more than a mere alternative to traditional welding tools—it is a transformational technology that redefines how welding and metal repairs are performed. Its unique combination of precision, speed, portability, and quality positions it as an essential tool for professionals who demand efficiency and excellence.
While it may not fully replace every traditional welding method in all circumstances, the hand held fiber laser welder unquestionably expands the boundaries of what is achievable. Its ability to operate in diverse environments and weld a wide range of metals without sacrificing quality makes it a must-have in modern metalworking.
Investing in this technology means stepping into the future of welding, equipped to meet the challenges of today’s demanding industries with confidence and innovation. The hand held fiber laser welder empowers welders to deliver outstanding results faster, cleaner, and more efficiently than ever before.