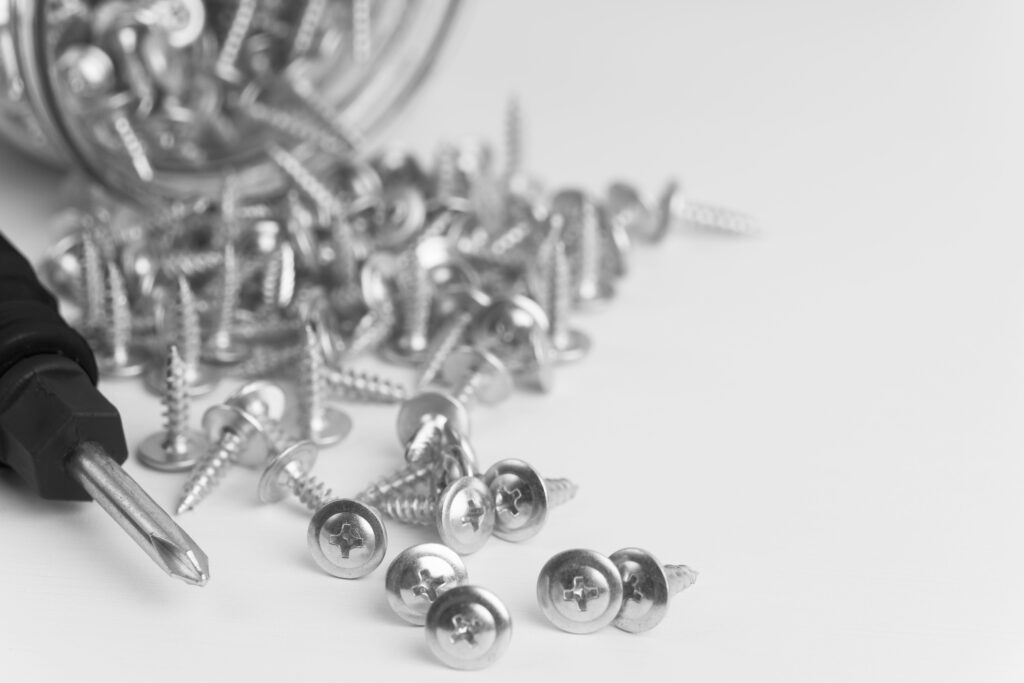
Multiple industries including construction and automotive and electronics and household appliance production depend on screws in their operations. The stability and extended product lifespan result from their ability to provide secure material fastening. To manufacture high-performance screw fasteners through this specialized procedure companies need engineering precision combined with advanced manufacturing equipment along with strict quality management systems.
This guide covers all stages of manufacturing screws starting with choosing raw materials through completing final finishing operations. This complete guide delivers beneficial information to both manufacturers seeking industrial knowledge and experts in the screw sector.
Raw Materials Used in Screw Manufacturing
The quality of screws depends largely on the raw materials used. The most commonly used materials in screw manufacturing include:
- Carbon Steel: Offers excellent strength and durability, making it ideal for machine screws and construction fasteners.
- Stainless Steel: Known for corrosion resistance, stainless steel screws are widely used in outdoor and marine applications.
- Brass: Used for electrical and decorative applications due to its non-corrosive nature and aesthetic appeal.
- Aluminum: Lightweight and resistant to corrosion, making it ideal for aerospace and automotive uses.
- Titanium: Highly durable and lightweight, often used in high-end industries such as medical, aerospace, and defense.
Screw manufacturers in Delhi and other industrial hubs source high-quality raw materials to ensure consistency and durability in their products.
Step-by-Step Screw Manufacturing Process
The screw manufacturing process involves multiple stages, each requiring precision and quality control. Here’s a detailed breakdown of the process:
- Wire Rod Preparation and Drawing
Manufacturing begins with the selection of top-quality metal wire rods which are usually delivered in large coils. The manufacturing process applies different methods to transform these rods until they reach the appropriate thickness requirements required for screw production. The first process commences with cleaning raw wire which removes rust, oil, dirt along with other impurities through wire rod cleaning. The wire surface remains contamination-free to prevent any negativity that might impact resulting quality levels of the finished product.
2. Cold Heading (Forging the Screw Head)
The material moves forward to cold heading processing only after manufacturers achieve the required wire thickness. The creation of different screw head types depends on the required use of the screw during this formation phase. A basic requirement in the process involves using proper equipment to cut wire samples into standard cylindrical shapes. The processes succeed or fail based on maintaining consistent dimensions since minor variations in length degrade the screw functions.
The cold heading machine receives the wire pieces before it shapes them through high pressure treatment while maintaining ambient temperature. The cold forging technique preserves material structural composition which results in strengthened products. The procedure also requires small changes to create spaces known as indentations or recesses that will help threading during later stages. The fastener market relies on cold heading technology because it delivers rapid mass-production together with high material strength in the screws.
3. Thread Rolling or Cutting
In screw manufacturing the essential creation of threads follows the previous operations because screws need these features to hold onto surfaces properly. Thread rolling and thread cutting stand as the main procedures for creating threads.
Most fastener manufacturers choose thread rolling since it both fortifies screws and maintains distinctive smooth edges. This technique locates the screw blank inside two dies that create the needed thread pattern through their pressing action. This production approach creates tightly organized threads that result in strong screws while preserving all the material supplied.
Thread cutting represents the production technique appropriate for screws fabricated from difficult materials which cannot achieve efficient rolling. A cutting tool eliminates material from the screw blank to create its threaded shape rather than using thread pressing methods. The production speed is reduced by this method yet it delivers precise results which explains why it is frequently chosen for aerospace, automotive and medical industry-specific fasteners.
4. Heat Treatment for Strength Enhancement
Screws become strong enough for mechanical usage and harsh environments through multiple heat treatment procedures which build their strength and durability properties. The beginning of hardening starts when screws enter a controlled furnace at elevated temperatures before experiencing quick cooling through oil or water. The fast arctic cooling process named quenching enhances material hardness which improves screw resistance toward wear damages.
The hardness level of screws reaches harmful brittleness through excessive heat treatments so the following process of tempering becomes required. The screws experience a spawned heating to an intermediate level followed by controlled temperature reduction. The material treatment enhances toughness which leads to reduced brittleness without compromising the gained strength. Heat treatment holds critical importance for screws operating in construction and heavy machinery sectors and aerospace applications because these sectors need enhanced mechanical qualities.
5. Surface Finishing and Coating
After heating and tempering the screws receive additional surface processing to develop their corrosion protection and aesthetic properties. The manufacturing sector employs multiple coatings with separate objectives.
Zinc plating represents the most extensively used surface treatment since it delivers both anti-corrosive protection and a reflective finish to screws. Laboratory professionals utilize this coating excellently for screws meant for outside exposure together with high humidity conditions. The black oxide coating serves two purposes by enhancing both visual appeal while offering relative protection against corrosion.
6. Quality Control and Testing
Various industry-standard quality control examinations determine whether the screws can be released for distribution. Quality control stands as an essential procedure that stops faulty screws from reaching end-users thus maintaining dependable operations and safe usage.
Dimensional accuracy testing begins by measuring screws through precise instrumentation to verify their property dimensions. Batches can meet the required standards because they are manufactured consistently. Subsequent to testing mechanical strength the procedure moves forward to evaluate how much load each screw can bear. Structural fasteners applied for construction and heavy-duty purposes require this specific test method for quality assurance.
7. Packaging and Distribution
The screws progress to their concluding phase after completing every necessary quality assessment before receiving packaging for distribution. The type of packaging used depends on where the screws are meant for sale. Large industrial outfits receive extensive packaging containing thousands of screws as a consolidated format for efficient manufacturing processes.
Manufacturer packaging of screws follows two different methods for retail along with DIY markets. First, products go into ready-to-sell kits, and second, these kits hold specified amounts with clear descriptions for buyer ease. Fasteners companies provide customized packaging solutions which match the unique requirements of businesses operating with specific industrial fasteners.
Choosing a Reliable Screw Manufacturer
A business must carefully choose its screw manufacturer to access premium fasteners since there are crucial implications. Key factors to consider include:
- You should verify that the manufacturer possesses state-of-the-art production infrastructure together with contemporary manufacturing tools.
- Customers should confirm that manufacturers use premium raw materials and execute extensive quality evaluation processes.
- The production of screws requires customization when particular businesses want distinctive products with particular material coatings and measurements.
- A manufacturer who has operated in the industry for many years will generate trustworthy screw fasteners.
- Select manufacturers which maintain conformance to standards ISO, DIN, and ASTM requirements.
Industrial hubs throughout Delhi together with other locations provide numerous manufacturing facilities that produce screws for different industrial requirements.
Conclusion
Manufacturing screws demands precise engineering together with high-quality materials across well-regulated quality control systems. The procedure of making screw fasteners includes wire drawing followed by heat treatment and ends with a coating step which fulfills essential functions for making reliable products. The manufacturing sector continues to change as both production operations and screw functionality receive improvements through emerging technologies.
Organization which deals with screws should collaborate with established screw manufacturers located in Delhi and other industrial areas to secure products that fulfill industry standards.