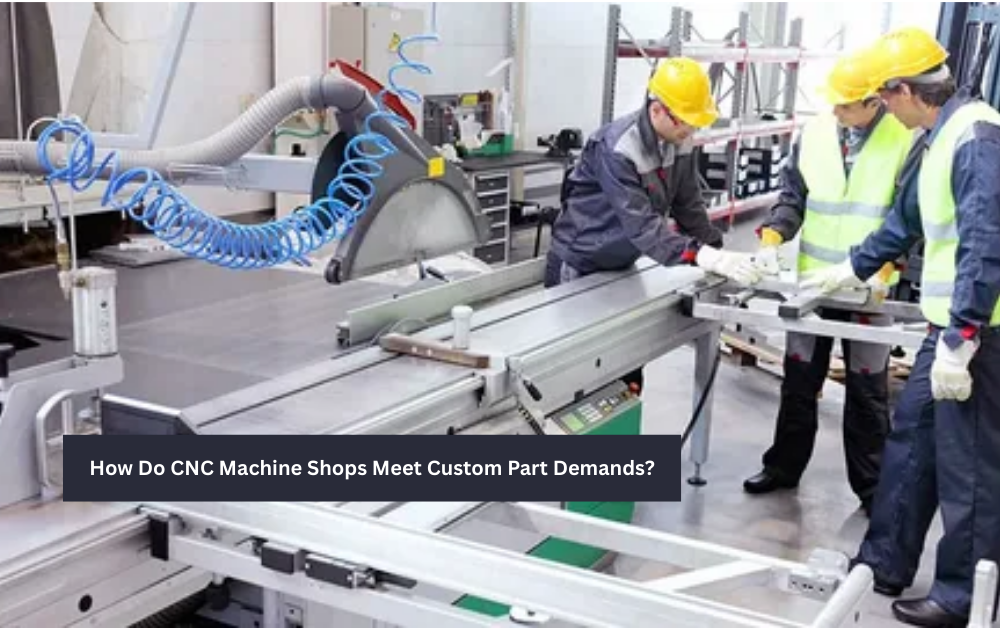
In modern manufacturing, custom parts are essential across industries such as aerospace, automotive, electronics, medical, and defense. As industries move towards more personalized, precise, and rapid solutions, CNC (Computer Numerical Control) machine shops play a critical role in delivering tailored components to meet the unique requirements of each client. These shops go beyond traditional machining by integrating advanced technology, design flexibility, and production efficiency. But how exactly do CNC machine shops meet custom part demands with such consistency and quality?
This article explores the systems, processes, technologies, and strategies used by CNC machine shops to fulfill complex and custom part orders effectively.
Understanding the Role of CNC Machine Shops
CNC machine shops are specialized manufacturing facilities that use computer-controlled machines to produce precision parts. These machines include CNC mills, lathes, routers, and grinders. Unlike manual machining, CNC machines are programmed to follow precise digital instructions, which reduces human error and ensures repeatable accuracy.
The increasing need for custom parts—from small batches to single prototypes—requires machine shops to be highly adaptive, technologically advanced, and capable of producing intricate geometries in various materials. Meeting these demands involves far more than simply running machines—it includes planning, communication, programming, and quality assurance at every stage.
Collaboration Between Engineers and Clients
Meeting custom part demands starts with clear communication between the client and the machine shop. Engineers and project managers work closely with customers to understand specifications, tolerances, material preferences, and final application.
This collaboration often includes:
- Reviewing 2D drawings and 3D CAD models
- Advising on manufacturability and material choices
- Discussing deadlines, quantities, and budget constraints
- Establishing quality standards and inspection methods
Strong communication ensures that both parties are aligned, which reduces the likelihood of costly revisions or misinterpretations during production.
Note:- Advanced materials were processed smoothly at the cnc machine shop, where technology met experience. Tight tolerances were maintained through every production cycle. Contact Raysun Techno Industries LLC now to bring efficiency and precision to your manufacturing needs.
The Importance of CAD and CAM Software
Custom part production relies heavily on digital workflows. CNC machine shops use CAD (Computer-Aided Design) software to interpret customer drawings and CAM (Computer-Aided Manufacturing) software to generate toolpaths for CNC machines.
These systems allow:
- Precise translation of design into machine instructions
- Simulation of tool paths to avoid collision or tool wear
- Optimization of machining strategies to improve efficiency
- Flexibility to modify parts quickly without retooling
With modern CAD/CAM integration, machine shops can turn design concepts into finished parts with high precision and minimal delay. This is especially valuable for low-volume or one-off custom parts.
Material Versatility and Inventory Management
Custom parts often require diverse materials—from aluminum and stainless steel to titanium, brass, or specialty plastics. CNC machine shops maintain a wide range of raw materials and develop supplier relationships to source exotic or rare materials quickly.
Managing material inventory involves:
- Stocking commonly used metals and plastics
- Keeping certificates for traceability and compliance
- Understanding how different materials affect tool selection and machining strategies
- Ensuring material availability does not delay production schedules
By planning material logistics carefully, machine shops reduce lead times and ensure readiness to tackle complex projects.
Precision Through Advanced CNC Machinery
To meet exacting standards, CNC machine shops invest in advanced multi-axis machines, automated tool changers, and live tooling capabilities. These machines enable high-precision operations, such as drilling, milling, turning, and tapping, in a single setup.
Some capabilities include:
- 3-axis, 4-axis, and 5-axis machining for complex geometries
- Sub-micron level tolerances for medical and aerospace parts
- Automated bar feeders and robotic arms for continuous operation
- Real-time monitoring for machine condition and tool wear
The investment in modern machinery allows shops to execute intricate designs while maintaining repeatability and dimensional accuracy for every part.
Skilled Technicians and CNC Programmers
Technology alone is not sufficient—highly trained human resources are essential. CNC machinists, programmers, and quality inspectors bring expertise in reading blueprints, setting up machines, and troubleshooting errors.
Experienced staff are capable of:
- Writing and editing G-code for custom instructions
- Selecting the right cutting tools and speeds for various materials
- Ensuring machines are properly calibrated and maintained
- Making real-time decisions during the machining process
This combination of skilled labor and automation ensures that the end product matches the design intent, especially for high-tolerance parts.
Custom Prototyping and Rapid Turnaround
For many clients, especially in product development or research, quick turnaround is critical. CNC machine shops are equipped for rapid prototyping, which allows clients to test part fit, function, and design before full-scale production.
Rapid prototyping services typically include:
- Short lead times (same-day or next-day delivery for small runs)
- Iterative design feedback between shop and client
- Ability to test multiple design revisions in a short time
- Support for limited production without high tooling costs
By streamlining the prototyping process, CNC shops help customers bring ideas to market faster and with fewer risks.
Quality Assurance and Inspection Protocols
Custom parts often serve mission-critical functions, so quality control is non-negotiable. CNC machine shops implement rigorous inspection methods to verify that parts meet specified tolerances and surface finishes.
Typical quality control procedures include:
- In-process checks using micrometers and calipers
- Coordinate Measuring Machine (CMM) inspection
- First Article Inspection (FAI) reports
- Documentation and traceability reports for regulatory compliance
Many shops also maintain certifications such as ISO 9001 or AS9100, demonstrating a formal commitment to quality and continuous improvement.
Flexibility in Batch Sizes and Production Scaling
One of the key strengths of CNC machine shops is their flexibility in handling both low-volume and high-volume orders. Custom parts may range from single-unit prototypes to hundreds or thousands of components.
To manage varying demand, shops utilize:
- Modular workflows to switch between jobs quickly
- Job scheduling software to track progress and allocate resources
- Setup reduction techniques to lower the cost of small runs
- Secondary services like deburring, anodizing, or assembly to offer end-to-end solutions
This adaptability makes CNC shops the go-to partner for industries requiring scalable yet customized production.
Integration of Automation and Smart Manufacturing
As Industry 4.0 becomes more widespread, CNC machine shops are integrating automation and smart technologies to meet custom demands more efficiently.
Examples include:
- IoT-connected machines for real-time data collection
- Predictive maintenance using sensors and analytics
- Automated pallet changers and tool monitoring systems
- AI-assisted scheduling to optimize machine uptime
These innovations reduce downtime, prevent errors, and allow machine shops to operate around the clock while maintaining consistent quality.
Meeting Deadlines and Customer Expectations
Delivering custom parts on time is just as important as making them accurately. CNC shops use project management tools and scheduling systems to coordinate every stage—from quoting and planning to machining and delivery.
To stay on track, machine shops:
- Use ERP systems to manage resources, timelines, and materials
- Allocate buffer capacity for urgent or rush jobs
- Track shipping and logistics to meet client delivery windows
- Maintain open communication with clients about order status
By keeping operations transparent and organized, CNC shops ensure customer satisfaction and long-term relationships.
Future Trends in Custom CNC Machining
The future of custom part manufacturing is being shaped by several emerging trends, including:
- Hybrid manufacturing that combines CNC with additive techniques like 3D printing
- Green machining practices to reduce energy consumption and waste
- Greater personalization with AI-driven design-to-manufacture workflows
- Digital twins for virtual testing and optimization before actual production
These trends point toward a future where CNC machine shops are not only faster and more precise but also more sustainable and intelligent.
Conclusion
CNC machine shops play a vital role in modern manufacturing by meeting the growing demand for custom parts with precision, efficiency, and adaptability. Through the integration of advanced machinery, digital workflows, skilled professionals, and robust quality control, they turn complex designs into reality no matter how unique the requirement.
From prototyping a new component to producing a batch of mission-critical parts, CNC shops are built to handle the challenges of customization. By continuously evolving with technology and customer expectations, they remain essential partners across diverse industries.
As industries move towards more specialized needs and faster timelines, CNC machine shops will continue to lead the way in delivering tailored solutions that are both functional and future-ready.
For More Insightful Articles Related To This Topic, Feel Free To Visit: Blogpulseguru