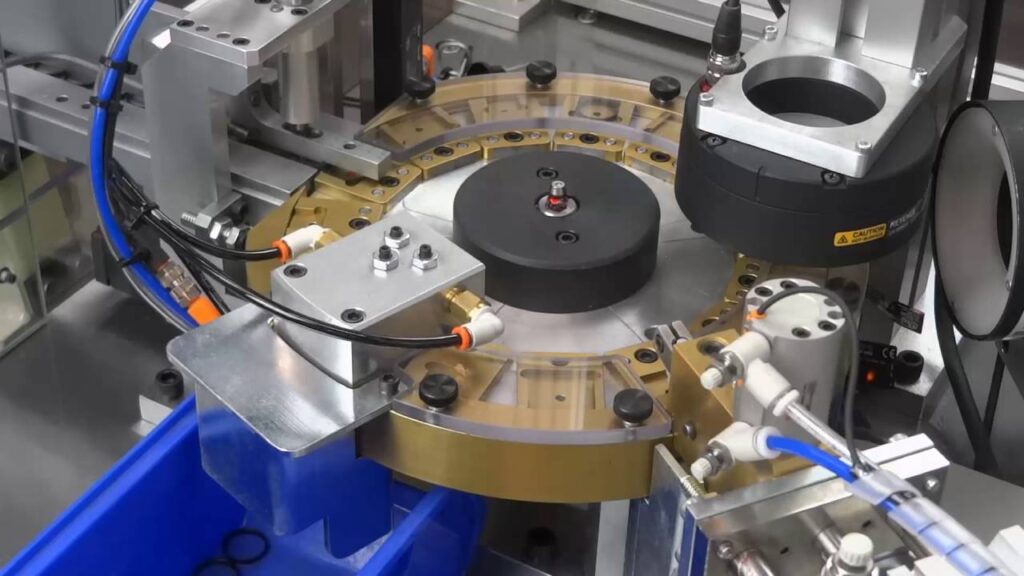
machine vision AOI
As manufacturers, we continually seek ways to enhance quality control and boost efficiency. When I first heard about machine vision AOI (Automated Optical Inspection), I was curious to see how it could enhance our manufacturing process. Along with AI Visual Inspection and the application of AI in visual inspection, these technologies promised to take our quality control system to the next level. Little did I know, incorporating these tools into our operations would make a significant difference. Here’s how I made my manufacturing process smarter with machine vision AOI and AI-based visual inspection.
NOTE: With the power of AI in visual inspection, we can stay ahead of production issues, improve customer satisfaction, and drive long-term growth. As technology continues to advance, we look forward to further enhancing our manufacturing process with even smarter systems. Machine vision AOI has truly made our operations smarter, and I can’t imagine going back to the old way of doing things.
What Is Machine Vision AOI, and Why Does It Matter?
Understanding Machine Vision AOI
Machine vision AOI is a technology that uses cameras and image processing software to inspect products in the manufacturing line. It automatically detects defects, verifies dimensions, and ensures the products meet quality standards. With machine vision AOI, the system doesn’t just check for visible flaws; it analyzes the items at a microscopic level, looking for imperfections or faults that human inspectors might miss.
How AI Visual Inspection Plays a Key Role
Incorporating AI Visual Inspection into the system adds another layer of intelligence. Instead of just relying on preset rules, AI allows the system to “learn” from past data. As it processes images, the AI improves its ability to detect various types of defects, even the ones that were previously hard to detect. This makes the system smarter and more adaptive, offering higher accuracy over time.
Why I Chose Machine Vision AOI for My Manufacturing Process
Improved Accuracy and Precision
Before implementing machine vision AOI, we relied heavily on manual inspections. While our team was diligent, the human eye simply couldn’t match the accuracy and precision of a camera system paired with advanced image processing. Small defects, like micro-cracks or slight deviations in size, often went unnoticed, which could lead to defective products reaching the customer.
With machine vision AOI, the system captures high-resolution images of each product and compares them to an ideal model. It uses software algorithms to detect even the smallest irregularities. AI in visual inspection helps further by identifying new defect patterns that weren’t initially programmed, allowing the system to get better over time.
Faster Inspection Process
One of the major challenges we faced was the speed of manual inspections. Quality control was slowing down our production line, as inspectors needed time to check each unit individually. With machine vision AOI, the inspection process became faster. The system works continuously, inspecting products as they move along the conveyor belt. This allows us to maintain a high level of quality without causing delays in production.
Reducing Human Error
Human error was a common issue in our previous manual inspection process. Inspectors could miss defects, get fatigued, or simply make mistakes. With AI Visual Inspection, this is no longer a concern. The machine vision system works tirelessly and consistently, ensuring that no defects are overlooked. It also doesn’t suffer from the fatigue or distractions that human inspectors might face.
How Machine Vision AOI and AI Visual Inspection Improved Our Operations
Better Resource Allocation
With machine vision AOI, we no longer needed a large team of inspectors to manually check each product. This freed up valuable resources that could be used elsewhere in the business. Instead of dedicating so many workers to quality control, our team could focus on higher-level tasks, improving overall productivity.
The time saved on manual inspections allowed us to scale up production without compromising on quality. AI in visual inspection helps optimize this process by fine-tuning the defect detection algorithm, ensuring that even the slightest flaws are detected without overburdening the system.
Real-Time Data and Analytics
One of the most valuable features of machine vision AOI is the ability to gather real-time data. The system doesn’t just detect defects; it also logs the data, giving us insights into patterns and trends. For instance, we can analyze which products are more likely to have defects and pinpoint the exact causes of failure. This information allows us to make immediate adjustments in our production process, preventing future issues.
AI Visual Inspection also adds predictive capabilities. It can forecast potential defects based on historical data, which means we can take preventive measures before problems occur. This proactive approach saves time, reduces waste, and improves product quality.
How I Integrated Machine Vision AOI into My Manufacturing Process
Step 1: Research and Selection
I started by researching the different types of machine vision AOI systems available in the market. I needed a solution that could integrate seamlessly with our existing production line. After narrowing down the options, I chose a system with AI Visual Inspection capabilities to ensure that the software could adapt and improve over time.
Step 2: Customization and Installation
Once the system was selected, the next step was customization. We worked closely with the vendor to tailor the system to our specific needs. The machine vision AOI system had to be configured to inspect our products at the right speed, accuracy, and resolution.
The installation process was smooth, with the vendor providing full support and training for our team. We also set up data monitoring tools to track system performance and ensure everything was running optimally.
Step 3: Continuous Improvement
After installation, the AI in visual inspection began to learn from the data it collected. Over time, the system became more accurate and efficient. As we continued to feed it data and fine-tune its algorithms, it became better at identifying subtle defects that even experienced inspectors might have missed.
Conclusion: The Impact of Machine Vision AOI and AI Visual Inspection
Integrating machine vision AOI and AI Visual Inspection into our manufacturing process was one of the best decisions we’ve made. The accuracy, speed, and consistency of the system have revolutionized our quality control process. It has not only improved product quality but has also allowed us to be more efficient, reducing waste and downtime.
For more insightful articles related to this topic, feel free to visit blogpulseguru