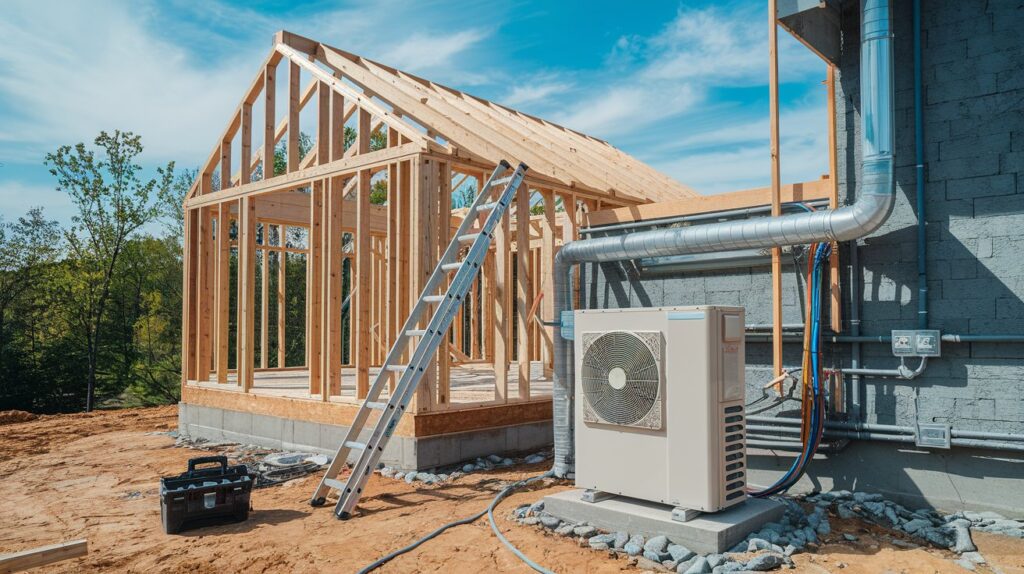
If there’s one part of industrial construction that consistently pushes budgets off track, it’s the MEP systems—mechanical, electrical, and plumbing. These aren’t the flashy parts of a facility, but they are the veins and arteries of its function. And they also account for a massive portion of total construction cost.
So why do so many project teams get MEP estimating wrong? Because the complexity is often underestimated, and the cost breakdown gets buried in generalized figures. That’s where Industrial Estimating Services come into play—offering the structure, clarity, and specificity required to bring precision to MEP projections in industrial builds.
Let’s demystify how to break MEP costs down effectively and bring a smarter, trade-aligned perspective into your next estimate.
MEP Complexity: More Than Just Utilities
In residential or even light commercial construction, MEP components are relatively straightforward. But industrial builds are a different beast. You’re not just dealing with basic HVAC or lighting. You’re looking at process cooling, compressed air lines, high-voltage systems, industrial waste drainage, explosion-proof installations, and more.
Each system interacts with others. HVAC often shares ceiling real estate with conduit. Plumbing layout affects electrical chase locations. And mechanical equipment may require custom foundations or structural reinforcement.
When these systems are priced in isolation or treated like checkboxes, surprises are guaranteed down the line.
Why You Need a Specialized Cost Breakdown
Too often, MEP is lumped together under one umbrella line item. The problem? It doesn’t reflect how labor, material, and equipment flow through the actual jobsite. Without clarity, it’s impossible to:
-
Spot overages early
-
Coordinate trades effectively
-
Plan phased installation efficiently
-
Bid accurately with subcontractors
A proper breakdown separates systems, scopes, and cost drivers—so decisions are informed, not reactive.
The First Layer: System-Level Cost Categories
Begin by categorizing each major system independently. This isn’t about line items yet—it’s about scope identification. Your MEP structure might look like this:
-
Mechanical: HVAC, process cooling, dust collection, steam piping
-
Electrical: Power distribution, lighting, data, controls, switchgear
-
Plumbing: Domestic water, sanitary waste, industrial fluids, gas piping
-
Fire Protection: Sprinklers, suppression systems, alarms
Each of these buckets carries its own codes, coordination needs, and procurement timelines. By starting here, you avoid the trap of over-generalizing.
Digging Deeper: Material, Labor, Equipment
Within each system, separate the costs into three buckets: material, labor, and equipment. Why?
Because each responds differently to design changes. For example:
-
Adding a booster pump might increase material cost slightly, but impact labor and equipment heavily.
-
A longer conduit run could dramatically raise labor but barely affect material pricing.
Breaking it down this way gives you better control. It also creates an internal audit trail—if one cost spikes, you can trace it back to its source rather than guessing where it went off course.
Don’t Overlook Prefabrication Potential
Modern industrial construction increasingly relies on prefabrication, especially for duct assemblies, conduit racks, or skid-mounted mechanical systems. A quality estimate should flag what portions of each MEP system can be prefabbed.
Why does this matter?
Because prefab changes the labor equation significantly. You may shift 40% of labor hours offsite, reduce install time, and tighten sequencing. This not only affects the labor line but also impacts equipment rental durations, safety costs, and supervision needs.
If your MEP estimate doesn’t consider prefab potential, it’s already outdated.
Hidden Cost Drivers Most Estimates Miss
In industrial builds, there are cost factors that aren’t listed on material invoices but show up in your final budget:
-
Rigging and craning for rooftop units or large switchgear
-
Specialty testing like duct leakage, water balance, or arc flash analysis
-
Permits and compliance documentation unique to process-heavy facilities
-
Commissioning labor—distinct from install labor and often not considered until late
These hidden costs should be clearly defined in the estimate and allocated to the appropriate trade or scope. If they’re buried in general conditions, they’ll get lost, leading to mid-project budget disputes.
Design-Build vs. Design-Bid-Build: Estimating Adjustments
The estimating strategy shifts depending on delivery method. For design-build, you’re often pricing from early narratives or schematic diagrams. The focus is on conceptual accuracy, allowances, and risk coverage.
For design-bid-build, you’re working from completed drawings—and precision is expected. Trade-specific detail, down to wire counts or valve locations, becomes critical.
Industrial estimating services adapt based on delivery method, ensuring that your level of detail matches your level of design certainty. The biggest mistake you can make is applying the same structure to both.
Labor Productivity Is Not a Flat Rate
Another trap: applying generic labor rates across all systems. Industrial work has unique site conditions, safety constraints, and skill demands. Welding stainless steel in a cleanroom is not the same as running copper pipe in a warehouse mezzanine.
Smart estimators adjust labor units based on environment, trade availability, shift timing (night vs. day), and installation sequencing. They also factor in local labor market conditions and union/non-union variables.
If you’re not recalibrating labor units based on actual conditions, you’re either overbidding and losing work—or underbidding and losing money.
The Power of Real-Time Updating
In fast-track industrial projects, design changes constantly. That means your estimate must be a living document—not a static PDF.
The best industrial estimating workflows allow for real-time updates. When a mechanical room grows or a panelboard moves, quantities shift. If your MEP cost breakdown can’t reflect that dynamically, you’re managing with outdated assumptions.
Modern industrial estimating services build estimates in layered structures that adjust with updates. This keeps procurement aligned and ensures field teams always operate off the latest cost model.
Communication: Turning Estimates Into Execution
Finally, your estimate must be understandable to more than just the finance team. Field managers, procurement leads, schedulers, and foremen should all be able to extract the information they need without decoding.
That’s where trade-aligned formatting matters. Clear cost tags, system codes, and descriptions let teams act on estimates—not just review them. The best estimates guide action on the ground, not just numbers on a screen.
The Bottom Line: Clarity Builds Confidence
MEP systems are complex, expensive, and highly interdependent. Yet most project risk still lies in how poorly they’re estimated.
By simplifying and clarifying the MEP cost breakdown through system-level thinking, trade-specific detail, and real-world insight, you gain control over the variables that derail so many industrial projects.
Industrial Estimating Services offer the methodology and experience to turn that complexity into clarity—giving you not just accurate numbers, but actionable intelligence.