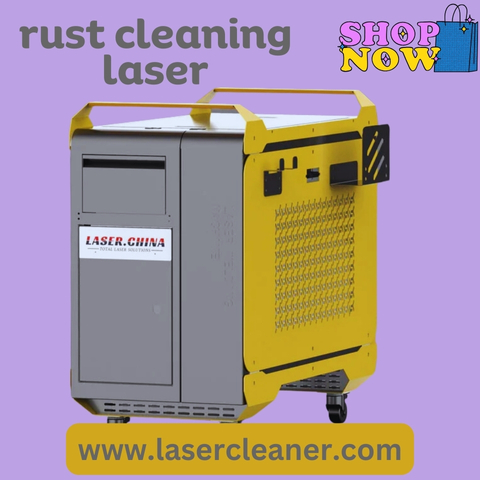
Cleaning rust from metal is not just about aesthetics—it’s about performance, longevity, and precision. But here’s the thing: traditional rust removal methods often miss the mark when it comes to deep, consistent surface restoration. That’s where the rust cleaning laser steps in as a modern solution built for accuracy and efficiency. If you’ve only relied on sandblasting, chemical agents, or abrasive scrubbing, you’re likely missing out on what a laser system can accomplish in a fraction of the time and with far greater surface integrity.
In this guide, we’ll take a detailed journey into what a rust cleaning laser actually does, how it changes the process of metal preparation, and why industries are quickly transitioning toward it—not as an upgrade, but as a necessity.
What Does a Rust Cleaning Laser Actually Do?
Let’s start by clearing the basics. A rust cleaning laser uses concentrated light energy to remove oxides (rust) and other contaminants from metal surfaces. It doesn’t scrape or chemically alter the metal—it evaporates the rust layer through controlled pulses. These pulses heat the rust at a micro level until it lifts off, leaving the original substrate untouched.
The process is often referred to as “laser ablation,” and it’s highly controlled, fast, and requires no secondary cleanup. Unlike sanding or blasting, there’s no dust cloud, no abrasive wear, and no need for chemical disposal. In highly sensitive industrial environments, this means the laser method is not only clean—it’s critical.
Why Surface Preparation Matters More Than You Think
You may be thinking, “I just want to remove rust, not build a spaceship.” But here’s the truth: rust removal is surface preparation, and if the base is flawed, everything that comes next—painting, welding, or coating—will fail over time. A rust cleaning laser isn’t simply about removing the visible red or brown coating; it’s about creating a pure surface ready for the next step in fabrication or restoration.
Industries like automotive, aerospace, and energy don’t tolerate flawed bonding or contamination. Even a micrometer of rust left behind can cause cracks or degradation in coatings. The laser eliminates this problem with precision, which is why it’s widely adopted in these fields.
The Hidden Cost of Traditional Rust Removal
Before lasers were mainstream, companies relied heavily on methods like grinding, sandblasting, or chemical baths. These systems have several unspoken issues:
-
Inconsistent removal
-
High labor costs
-
Environmental compliance complexity
-
Secondary waste generation
-
Tool wear and surface damage
These aren’t just minor inconveniences—they’re cost drivers. You end up spending more money fixing what a less-accurate system left behind. The rust cleaning laser solves these hidden costs by operating with minimal maintenance, no consumables, and reduced labor input. That means one operator with a handheld unit can do what used to take a team of workers and several steps.
Industries Already Using Rust Cleaning Lasers
While you might associate lasers with high-tech labs or electronics manufacturing, they’ve found a practical home in a range of heavy-duty industries:
-
Shipbuilding: Removing rust and marine buildup on steel hulls without damaging weld lines.
-
Rail: Surface prep for repainting, without disassembling equipment.
-
Military and Defense: De-rusting weapon parts or vehicle panels without altering mechanical tolerances.
-
Automotive Restoration: Stripping classic car frames back to clean metal while preserving detail.
-
Manufacturing Plants: Cleaning molds and dies without stopping production lines.
This widespread use isn’t just trend-following—it’s problem-solving.
Rust Cleaning Laser vs. Conventional Cleaning: A Process Breakdown
Let’s visualize the typical steps in both traditional and laser cleaning processes:
Traditional Rust Cleaning
-
Disassemble parts
-
Apply solvent or sandblast
-
Manually scrub or polish remaining spots
-
Rinse and dry
-
Reassemble and inspect
-
Repeat if needed
Laser Rust Cleaning
-
Direct laser beam at surface
-
Rust evaporates instantly
-
Surface remains cool and untouched
-
Move to next part—no downtime
-
No extra steps
Laser cleaning simplifies the process from a six-step routine to a two-step operation with zero consumables and minimal residue.
Safety and Precision Go Hand in Hand
One of the most underrated aspects of using a rust cleaning laser is safety. Traditional methods involve harsh chemicals that pose risks to operators and require hazardous waste management. Blasting and grinding create airborne particles, which require PPE, ventilation systems, and compliance reporting.
Laser systems, on the other hand, are designed with enclosed beams or safe open-area configurations. They’re often integrated with fume extractors to remove vaporized material and are much safer for long-term operator use.
The bonus? You don’t sacrifice precision for safety. These systems target only the rust layer, leaving paint, coatings, or sensitive geometry intact if programmed correctly.
Maintenance and Operation: What You Need to Know
Operating a rust cleaning laser doesn’t require a team of engineers. Most models come as plug-and-play units with handheld interfaces or robotic arms. Regular maintenance involves lens cleaning, checking fiber connections, and updating firmware—minimal compared to the oiling, abrasive refills, and filter replacements needed in traditional systems.
Also, since there are no consumables involved (no grit, no pads, no chemicals), operational costs become more predictable. You know your power usage, your laser pulse cycle count, and your uptime, down to the hour.
Long-Term Value in Industrial Workflow
This is where the rust cleaning laser truly shines—integration into industrial systems. Whether it’s pre-weld cleaning, surface prep before painting, or routine maintenance, these lasers can be incorporated into conveyor lines, robotic arms, or mobile cleaning stations.
That makes it more than a cleaning tool. It becomes part of your workflow optimization strategy. With programmable settings, repeatable results, and consistent energy consumption, it’s a machine that pays for itself in uptime and quality assurance.
Is It Worth the Investment?
Think about what rust does: it slows down production, weakens components, increases failure rates, and adds unnecessary labor. Now think about a system that reverses all that with a single tool.
While a rust cleaning laser may have a higher entry cost, the total ownership cost often ends up lower over time. You save on:
-
Chemical purchases
-
Waste disposal
-
Labor hours
-
Safety equipment
-
Downtime due to cleaning steps
For businesses that deal with frequent rust buildup, especially in harsh environments, the return on investment isn’t speculative—it’s measurable.
Final Thoughts
A rust cleaning laser is no longer a futuristic tool—it’s a practical solution reshaping how industries approach surface preparation. From precision to productivity, it delivers a method that doesn’t just clean metal, but prepares it for performance and reliability. If you’re serious about quality and process control, and if rust is a recurring problem in your workflow, then a laser-based solution isn’t optional—it’s essential.
Whether you’re restoring classic components or running high-output production lines, consider what your current rust cleaning process is costing you—not just in material, but in time and potential. A rust cleaning laser might be the missing piece that transforms your entire approach.