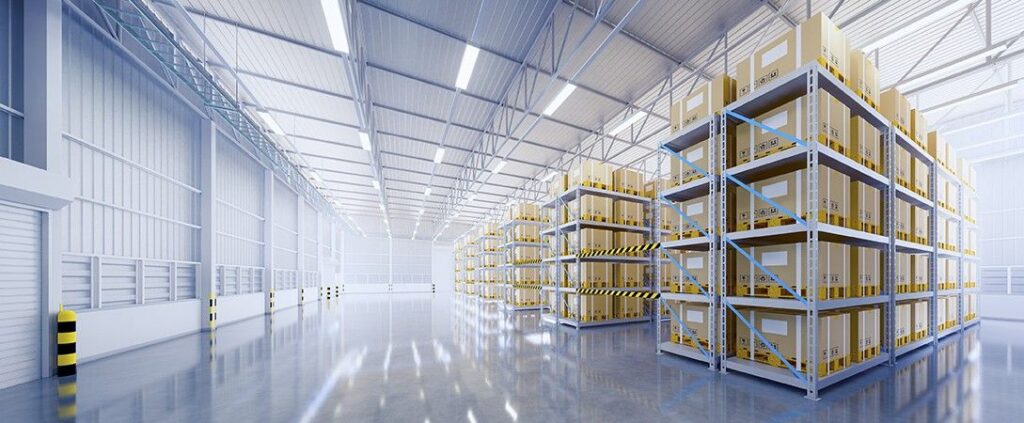
In today’s fast-paced logistics and supply chain environment, warehouse operations are under constant pressure to be more efficient, accurate, and scalable. One powerful strategy that helps achieve these goals is warehouse mapping. Often overlooked, warehouse mapping is a critical process that enhances visibility, improves inventory management, and streamlines workflows.
This article explores the concept of warehouse mapping, its benefits, essential components, implementation strategies, and how it can transform warehouse efficiency in 2024 and beyond.
What is Warehouse Mapping?
Warehouse mapping refers to the process of creating a detailed layout or blueprint of a warehouse, highlighting the location of storage areas, inventory zones, equipment, aisles, docks, and other critical assets. This map acts as a visual guide for warehouse staff and systems, ensuring that products can be stored, located, and retrieved efficiently.
It goes beyond simple floor plans—modern warehouse mapping incorporates digital tools, real-time data, and integration with Warehouse Management Systems (WMS) to provide dynamic, data-driven insights.
Why is Warehouse Mapping Important?
1. Enhanced Inventory Visibility
With a precise warehouse map, staff can easily locate any item in real-time, reducing time spent searching for misplaced stock and improving overall productivity.
2. Improved Order Accuracy
Warehouse mapping supports picking and packing operations by guiding workers to the right location quickly, which minimizes errors and enhances order fulfillment rates.
3. Optimized Storage Utilization
Mapping helps identify underused or overcrowded areas, allowing better space allocation and maximising the use of available square footage.
4. Streamlined Workflow
A well-mapped warehouse reduces travel time, supports logical product placement, and allows smooth coordination between different departments or teams.
5. Simplified Training
New employees can be trained faster using a visual representation of the warehouse layout, which improves onboarding efficiency and reduces dependency on experienced staff.
Components of a Warehouse Map
To create a comprehensive warehouse map, several components must be included:
✅ Storage Locations
These include racks, bins, shelves, pallets, mezzanines, and any designated product zones. Each location should be labeled and tracked within a WMS.
✅ Aisles and Travel Paths
Efficient path mapping reduces congestion and travel time for picking and restocking operations.
✅ Inbound/Outbound Docks
Clear identification of receiving and shipping zones is vital for coordinating inbound and outbound logistics.
✅ Equipment Zones
Include forklift parking areas, battery charging stations, and conveyor systems.
✅ Staging and Packing Areas
These zones are critical for quality checks, packaging, and preparing orders for dispatch.
✅ Safety Zones
Fire exits, first aid kits, emergency assembly points, and other safety-related areas should be clearly marked.
How to Implement Warehouse Mapping
Step 1: Assess Current Layout
Begin with a detailed audit of your current warehouse layout, noting storage capacities, bottlenecks, and existing workflows.
Step 2: Choose a Mapping Tool
Use digital warehouse mapping tools or CAD software integrated with your Warehouse Management System. Modern WMS platforms often come with built-in mapping features.
Step 3: Define Zones and Locations
Break down the warehouse into manageable zones (e.g., Aisle 1, Zone A1, Rack B2), and assign location codes to each storage area.
Step 4: Incorporate Real-Time Data
If your warehouse uses automation or IoT devices, feed real-time data into the map to reflect inventory movement, availability, and task completion.
Step 5: Train Staff and Integrate into Operations
Once implemented, train staff to use the map for navigation, picking, and inventory tasks. Ensure it’s easily accessible via handheld devices or printed guides.
Benefits of Digital Warehouse Mapping
While traditional warehouse mapping using paper floor plans is a start, digital mapping solutions offer far greater advantages:
✔ Real-Time Location Tracking
Digitally mapped warehouses integrated with barcodes, RFID, and IoT can track item movement in real time, ensuring precise location data.
✔ Integration with WMS and ERP Systems
Warehouse mapping works seamlessly with backend systems to synchronize inventory updates, replenishment, and order fulfillment.
✔ Heatmaps and Analytics
Advanced platforms can generate heatmaps showing traffic patterns, picking frequency, and idle zones—valuable insights for layout optimization.
✔ Scalability
As your business grows, digital mapping allows quick updates and modifications without starting from scratch.
Warehouse Mapping and Automation
Warehouse mapping is a foundational requirement for implementing automation. Whether you’re deploying Automated Guided Vehicles (AGVs), robotic picking systems, or drone inventory checks, a detailed warehouse map ensures that automation technologies can navigate and operate accurately.
Some of the technologies that benefit from warehouse mapping include:
-
Pick-to-Light and Put-to-Light Systems
-
Automated Storage and Retrieval Systems (ASRS)
-
Voice Picking Solutions
-
Mobile Robots and Drones
By synchronizing real-time maps with these technologies, you improve precision, reduce errors, and accelerate ROI.
Warehouse Mapping Best Practices
To make the most of your warehouse mapping strategy, consider these best practices:
🔹 Keep It Updated
Warehouses are dynamic environments. Regularly update your map to reflect layout changes, new equipment, or modified storage zones.
🔹 Involve Your Team
Engage warehouse staff when designing or modifying the map. Their on-the-ground insights are invaluable for identifying inefficiencies.
🔹 Use Clear Labelling
Ensure that all areas on the map are clearly labeled and that corresponding signs in the physical space match the digital layout.
🔹 Monitor KPIs
Use data from your mapped warehouse to track KPIs like pick rate, travel time, order accuracy, and inventory turnover.
🔹 Plan for Future Expansion
Design your warehouse map with future scalability in mind—anticipating new product lines, automation, or layout changes.
Industries That Rely on Warehouse Mapping
🏭 E-commerce & Retail
In fast-paced retail environments, accurate warehouse mapping is critical for managing SKU-heavy inventories and rapid fulfillment.
💊 Pharmaceuticals
Temperature-sensitive products, controlled substances, and tight regulations require precise tracking and documentation via mapping tools.
🍎 Food and Beverage
Mapped warehouses ensure FIFO (First-In-First-Out) inventory rotation, cold chain management, and allergen segregation.
🛠️ Manufacturing
Assembly components, work-in-progress inventory, and finished goods all require streamlined movement, enabled by warehouse maps.
Future of Warehouse Mapping
The future of warehouse mapping lies in greater digitization, automation, and AI-driven analytics. Emerging trends include:
-
3D warehouse mapping for visualizing vertical storage solutions
-
AR/VR mapping tools for immersive training and navigation
-
AI-powered route optimization for dynamic task allocation
-
Digital twin technology, replicating the warehouse virtually for real-time simulation and planning
These innovations will transform warehouse mapping from a static tool into a live, intelligent asset that drives decision-making.
Conclusion
In the modern warehouse, warehouse mapping is no longer optional—it’s a strategic necessity. It supports operational efficiency, inventory accuracy, regulatory compliance, and the seamless integration of automation and analytics.
By implementing a comprehensive warehouse mapping strategy, businesses can reduce waste, lower costs, and deliver better service to customers in an increasingly competitive landscape.
Whether you’re just starting your optimization journey or upgrading an existing system, accurate and dynamic warehouse mapping is your blueprint for success.