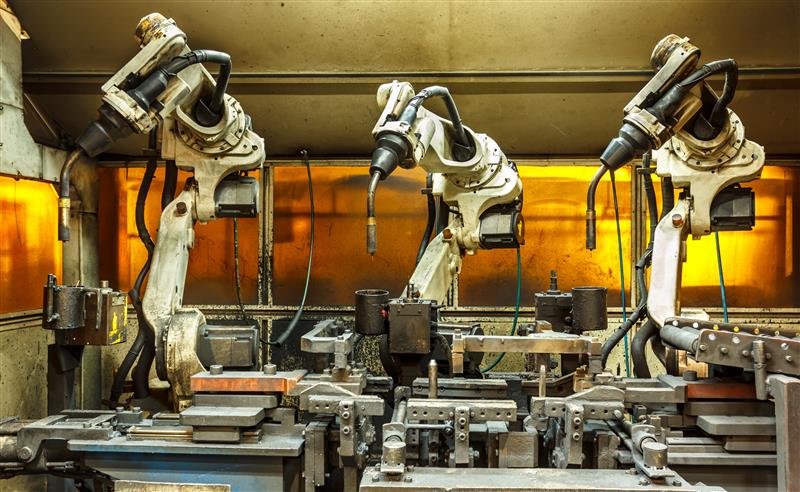
Industrial Automated Systems
Pharmaceutical manufacturing is one of the most tightly regulated, high-stakes industries on the planet. Every tablet, vial, or dose has to meet strict safety and quality standards. That’s why more and more pharmaceutical companies are turning to industrial automated systems to streamline their processes, minimize errors, and stay compliant.
If you’re new to the topic or want to see how automation is shaping this space, check out this detailed overview of Industrial Automated Systems.
In this article, we’ll explore how pharmaceutical production and industrial automation are not just compatible—they’re a perfect match.
Why Automation Is Critical in Pharma
Let’s face it—there’s zero room for error in pharma. A single mistake in formulation or packaging can mean serious health consequences, product recalls, or regulatory penalties. Automation helps eliminate human error by delivering precise, consistent, and repeatable processes from start to finish.
And it’s not just about accuracy. It’s also about speed, traceability, compliance, and cost efficiency—all areas where automated systems shine.
Streamlining Formulation and Mixing
Creating consistent drug formulas at scale is no small feat. With automated dosing and mixing systems, pharmaceutical manufacturers can precisely control:
-
Ingredient quantities
-
Mixing times and temperatures
-
Batch-to-batch consistency
This improves not only product quality but also compliance with Good Manufacturing Practices (GMP) and FDA requirements.
Precision in Filling and Packaging
Filling capsules, vials, or blister packs is a process that demands both speed and accuracy. Industrial automated systems help with:
-
Precise liquid or solid dosage filling
-
Sealing and capping
-
Labeling and serialization
This ensures that every unit is identical and traceable—which is especially crucial in case of recalls or audits.
Automation also reduces product loss, which adds up to significant cost savings in the long run.
Enhancing Sterility and Contamination Control
Contamination is a serious concern in pharmaceutical environments. Human involvement—even with protective gear—introduces risk.
Automated systems reduce human touchpoints and operate within cleanroom environments, minimizing contamination and improving product sterility. In aseptic processing, automation isn’t just helpful—it’s essential.
Real-Time Monitoring and Quality Control
Quality control is no longer a separate step—it’s built directly into the process through real-time sensors and monitoring systems.
These tools allow manufacturers to:
-
Detect anomalies immediately
-
Adjust variables during production
-
Maintain detailed electronic records for audits
When your systems are constantly watching and adjusting themselves, your product quality goes up—and your headaches go down.
You can dive deeper into automation-enhanced monitoring tools through this smart quality control resource.
Batch Record Automation for Compliance
Every pharmaceutical batch needs a paper trail—or more accurately, a digital trail. Automated systems can generate and store electronic batch records (EBRs), making it easier to:
-
Stay compliant with 21 CFR Part 11
-
Provide instant documentation during inspections
-
Trace every step of the production process
Automated record-keeping is a massive time-saver and dramatically reduces the chance of documentation errors.
Accelerating Time to Market
Speed matters. Whether it’s responding to market demand or rolling out a new drug, time to market is crucial.
Industrial automated systems slash delays caused by manual processes, human bottlenecks, and rework. By increasing process efficiency, automation gives pharmaceutical companies a real competitive edge.
Lowering Operational Costs
At first glance, automation seems like a hefty investment—and to be fair, it can be. But the long-term savings are substantial. With fewer errors, less waste, faster production, and reduced labor costs, automation pays for itself over time.
And when you factor in the cost of non-compliance or recalls? Automation looks even more appealing.
Improving Worker Safety and Ergonomics
Pharmaceutical manufacturing isn’t just mentally demanding—it can also involve repetitive or physically intense tasks. Automated systems take over the tedious and risky jobs, letting human workers focus on oversight and problem-solving.
That translates to fewer injuries, higher job satisfaction, and a more productive workforce.
Scalability for Future Growth
One of the most attractive benefits of automated systems is scalability. Whether you’re a contract manufacturer producing small batches or a large pharma company with global distribution, automation grows with you.
You can add production lines, update processes, or expand into new product types without starting from scratch—just reprogram and go.
Choosing the Right Automation Partner
Not all systems are created equal. To truly benefit from automation, you need a provider who understands the unique challenges of pharmaceutical production. Look for a partner experienced in industrial automated systems services that comply with GMP, FDA, and international standards.
They should offer:
-
End-to-end integration
-
Ongoing support and training
-
Scalable and flexible system design
-
Experience in pharma-specific applications
The right partner doesn’t just sell you equipment—they help you succeed.
Final Thoughts: A Future Built on Precision
Automation isn’t just a trend—it’s the backbone of modern pharmaceutical production. As regulatory demands increase and patient safety remains paramount, automation gives manufacturers the tools to deliver with precision, confidence, and speed.
Whether it’s maintaining sterility, improving consistency, or slashing production times, the match between pharmaceutical production and industrial automated systems couldn’t be more perfect.