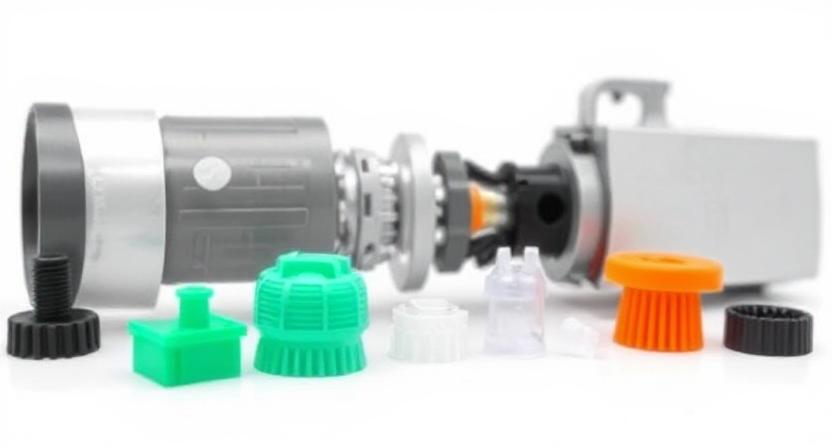
Plastic injection molding stands as one of the most versatile and widely used manufacturing processes across industries today. This efficient method produces high volumes of identical plastic parts with remarkable precision, making it indispensable for everything from medical devices to automotive components.
The process involves injecting molten plastic material into a custom mold cavity under high pressure, where it cools and solidifies into the desired shape. With capabilities ranging from micro-sized components to large industrial parts, injection molding offers unmatched repeatability, cost-effectiveness at scale, and design flexibility that few other manufacturing methods can match.
Why Plastic Injection Molding Dominates Manufacturing
1. Unparalleled Efficiency for High-Volume Production
Once the initial mold is created, Plastic injection molding machines can produce thousands – even millions – of identical parts with minimal variation. The cycle times are incredibly fast, often measured in seconds, allowing for mass production that keeps unit costs remarkably low. This makes the process ideal for:
- Consumer products (bottle caps, containers)
- Automotive components (dashboards, bumpers)
- Medical supplies (syringes, surgical instruments)
Modern injection molding machines feature advanced automation, with robotic arms removing finished parts and preparing for the next cycle without human intervention, further boosting productivity.
2. Exceptional Material Versatility
Injection molding accommodates an extraordinary range of thermoplastic and thermoset materials, each offering unique properties:
- Common Thermoplastics:
- ABS (durable, impact-resistant)
- Polypropylene (chemical resistant, flexible)
- Polycarbonate (transparent, high-strength)
- Engineering-Grade Plastics:
- PEEK (high-temperature resistance)
- Nylon (wear-resistant, durable)
Material selection can be tailored to meet specific requirements for strength, flexibility, chemical resistance, or biocompatibility, making injection molding suitable for virtually any application.
3. Precision and Repeatability
Modern injection molding achieves tolerances as tight as ±0.005 inches, with consistent results across production runs. Advanced features like:
- Multi-cavity molds (producing multiple parts per cycle)
- Hot runner systems (reducing material waste)
- Gas-assisted injection (for hollow parts)
enable manufacturers to create complex geometries with intricate details that would be impossible or prohibitively expensive with other methods.
4. Cost-Effectiveness at Scale
While the initial tooling investment can be significant, the per-unit cost becomes extremely competitive at higher volumes. Factors contributing to cost efficiency include:
- Minimal material waste (runners and sprues can often be recycled)
- Reduced labor requirements (thanks to automation)
- Long mold lifespan (typically 100,000+ cycles for steel molds)
This makes injection molding the go-to choice for products requiring high-volume production with consistent quality.
Key Industries Relying on Injection Molding
The versatility of plastic injection molding makes it critical to numerous sectors:
Medical Industry:
- Sterile, single-use devices
- Implantable components
- Diagnostic equipment housings
Automotive Sector:
- Interior and exterior trim
- Under-the-hood components
- Connectors and electrical parts
Consumer Electronics:
- Device housings
- Buttons and switches
- Cable management components
Packaging Applications:
- Closures and caps
- Thin-walled containers
- Custom dispensing systems
Choosing an Injection Molding Partner
Selecting the right injection molder requires careful consideration of several factors:
Tooling Expertise:
- Mold design capabilities
- Experience with complex geometries
- Knowledge of gate and runner optimization
Production Capacity:
- Range of press sizes (tonnage)
- Automation capabilities
- Secondary operations (assembly, decorating)
Quality Systems:
- ISO certification
- Process validation protocols
- Quality control measures
Material Knowledge:
- Resin selection guidance
- Specialty material experience
- Regulatory compliance (FDA, USP Class VI)
Future Trends in Injection Molding
The injection molding industry continues to evolve with several exciting developments:
Industry 4.0 Integration:
- Real-time process monitoring
- Predictive maintenance systems
- AI-driven quality control
Sustainable Practices:
- Biodegradable material options
- Energy-efficient machines
- Closed-loop recycling systems
Advanced Technologies:
- Micro-injection molding
- Multi-material molding
- In-mold electronics
Conclusion
Plastic injection molding remains the gold standard for mass production of plastic components, offering an unbeatable combination of efficiency, precision, and cost-effectiveness. As materials and technologies continue to advance, its applications will only expand further into new industries and product categories.