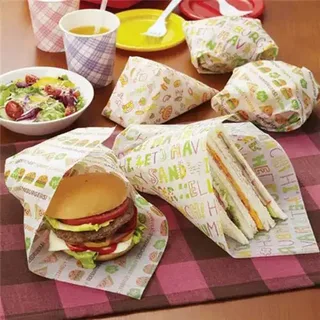
Custom Sandwich Paper
Custom sandwich paper is nowadays an indispensable element of packaging in the foodservice industry that has evolved beyond its traditional functional appearance. Not only do these papers lead to hygiene and freshness, but they also provide special branding value. With the increasing concern about company brand exposure and sustainability, it can be insightful to know something about the production process of custom sandwich paper.
Whether it is the choice of material for the logo printing and wholesale provision, the stages have been designed in such a way that the design is made to be functional yet appealing. Through this article, we guide you about how custom sandwich papers are manufactured as well as how they help the food brands of various industries achieve success.
Choosing Base Material
To begin with, one selects high-quality paper, which is normally of food-grade kraft, wax, custom sandwich paper. These may include materials that are grease-resistant, strong, and eco-friendly. It pays great attention to food safety compliance, and the manufacturers make sure that the paper conforms to the FDA or CFIA requirements. This base determines the resistance and elasticity of the individual sandwich paper bags that one can use in wrapping various kinds of sandwiches and snacks.
Branding Designs
After selecting the paper material, it is the turn to design the artwork. The design firms collaborate with the businesses to design tailor-made layouts with a branding element like logo, slogan, color scheme, or even patterns. They are designed to allow repeat printing so that the brand name will be seen; however, the paper might be folded or wrapped. It is here that custom sandwich paper with a logo can help because the association with the logo becomes necessary to drive home the visual identity each time a customer is contacted.
Printing Plates Preparation
On bulk orders, manufacturers adopt the flexo-graphic or the offset printing, where they make the printing plates. The engraved versions of these designs are printed on these plates, which assist in the uniform application of ink to the paper. These plates also bear a direct influence on the sharpness and ability of accurate color of custom-printed sandwich paper. After a preparation of the plates have been prepared, they are put on the press to continue with the next process.
The Paper Printing
The chosen designs are put into operation during the printing phase and using food-safe, water-based inks, on large rolls of sandwich wrapping paper. The inks are non-toxic and are not smudged or greasy, bearing clarity during use. Fast printers also handle unwound continuous rolls, ensuring unending consistency and accuracy. The process can enable the wholesalers of custom sandwich paper to deal with the large quantities with efficiency and uniformity.
Protective Coating Addition
A light application can be done to improve the performance, depending on the final use. There are choices such as using wax to make it moisture-proof or grease barriers that are biodegradable to suit environmentally friendly brands. These coatings also make sure that the sandwich wrap paper does not tear and leak in case we use it with juicy or oily food items. They both need to be coated, as this is related to usability and retaining a visual appeal during transportation and consumption.
Trimming and Sizing Sheets
As soon as the printing and coating are done, the rolls are taken to cutting machines where the paper is cut into various sizes required. Depending on the needs of the clients, sizes can differ, both as wraps or liners, or 10×10 or 12×12 inches are common. This step has to be done with precision to prevent wastage and also to make the custom sandwich paper sheets to suit the packaging or the tray.
Quality Control Tests
Each batch is thoroughly checked before it is packaged. Inspectors check the alignment of prints, consistency of ink, as well as coating performance. The grease resistance of paper and durability to withstand the requirements of the commercial kitchen are also examined. This will ensure that each unit of custom sandwich paper with a logo will meet the expectations of customers regarding the brand. The quality control in this step ensures few reprints and confidence among wholesale customers.
Distribution and Packaging
Lastly, the completed sandwich papers are prepared into neat stacks or rolls, and they are then packed in moisture-resistant cartons, and they follow a labeling procedure before shipping. Custom boxes wholesale distributors customize orders placed by restaurants or by companies that would have different franchise restaurants and prepare bulk supplies according to the schedule of the client. Such boxes are also optimized in terms of storage, where space consumption is minimized and allowing long shelf life. Most suppliers are providing environmentally friendly packages to support green branding efforts.
Conclusion
The design life of a custom sandwich paper presents a concerted harmony between shape and utility. Whether they are picking food-safe materials, personalized branding, excellent printing, or an efficient volume delivery, all of these things are important to the delivery of a predictable and professional product. This is because the papers, besides being effective ways to protect food and maintain hygiene, are also an effective branding tool.
This orderly production process can also be resorted to by business firms planning to improve their packaging experience in a competitive food industry. As little details and creativity are added, the custom sandwich paper will not be a mere wrap anymore; it will be a brand ambassador.