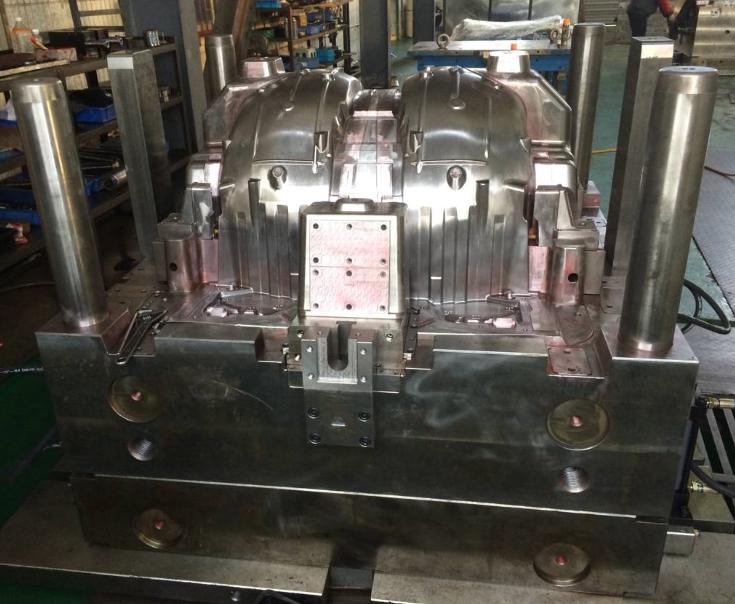
Understanding Polycarbonate and ABS Injection Molding
Injection molding is a widely used manufacturing process. It allows for the production of complex parts from various materials. Two popular materials in this process are polycarbonate and ABS (Acrylonitrile Butadiene Styrene). This article will explore what these materials are, the injection molding processes for each, their benefits, and their applications.
What is Polycarbonate Injection Molding?
Polycarbonate injection molding involves using polycarbonate resin to create parts through the injection molding process. Polycarbonate is a durable thermoplastic known for its high impact resistance and optical clarity. This makes it suitable for various applications, from eyewear lenses to automotive components.
Advantages of Polycarbonate Injection Molding
- High Strength and Durability: Polycarbonate parts can withstand significant stress and impact. This makes them ideal for applications that require toughness.
- Transparency: Polycarbonate is naturally transparent, allowing for light transmission. This property is beneficial for products like light covers and lenses.
- Heat Resistance: Polycarbonate can handle high temperatures without deforming, making it suitable for applications exposed to heat.
- Versatility: It can be molded into various shapes and sizes, accommodating diverse design requirements.
Applications of Polycarbonate Injection Molding
Polycarbonate injection molding is used in various industries. Here are some common applications:
- Automotive Parts: Headlight lenses, dashboards, and interior components benefit from polycarbonate’s strength and clarity.
- Electronics: Housings for electronic devices often utilize polycarbonate for its durability.
- Medical Devices: Due to its clarity and safety, polycarbonate is used in medical equipment and devices.
- Safety Equipment: Helmets and protective gear frequently use polycarbonate for its impact resistance.
What is ABS Injection Molding?
ABS injection molding uses ABS resin to create parts through the injection molding process. ABS is a thermoplastic known for its toughness and impact resistance. It is widely used in various applications due to its excellent mechanical properties.
Benefits of ABS Injection Molding
- Impact Resistance: ABS is known for its ability to withstand impacts, making it suitable for applications where durability is essential.
- Easy to Paint and Finish: ABS parts can be easily painted or finished, allowing for aesthetic customization.
- Good Chemical Resistance: ABS has good resistance to many chemicals, making it suitable for various environments.
- Cost-Effective: Compared to other materials, ABS is often more affordable, making it a popular choice for manufacturers.
Applications of ABS Injection Molding
ABS injection molding finds applications across multiple industries. Here are some key areas where ABS is commonly used:
- Consumer Goods: Items like toys, appliances, and cases often use ABS due to its durability and ease of production.
- Automotive Components: ABS is used in various automotive parts, including interior trim and dashboard components.
- Electronics: Housings for various electronic devices frequently utilize ABS for its impact resistance and easy finishing.
- Industrial Applications: ABS is used in manufacturing tools, machinery parts, and other industrial components.
Comparing Polycarbonate and ABS Injection Molding
When choosing between polycarbonate and ABS for injection molding, consider the following factors:
Feature | Polycarbonate | ABS |
---|---|---|
Strength | High impact resistance | Good impact resistance |
Transparency | Naturally transparent | Opaque |
Heat Resistance | Excellent heat resistance | Moderate heat resistance |
Cost | Generally higher cost | More cost-effective |
Finish | Can be polished | Easy to paint and finish |
Key Differences
- Transparency: Polycarbonate is transparent, while ABS is opaque. This makes polycarbonate suitable for applications requiring visibility.
- Cost: ABS is usually more affordable than polycarbonate, making it a go-to choice for budget-sensitive projects.
- Heat Resistance: Polycarbonate can withstand higher temperatures compared to ABS, which may deform under extreme heat.
The Injection Molding Process
Both polycarbonate and ABS injection molding follow a similar process. Here’s a step-by-step breakdown:
- Material Preparation: The plastic resin is dried and prepared for injection. This step is crucial, especially for polycarbonate, which can absorb moisture.
- Injection: The resin is heated until it melts and then injected into a mold under high pressure. This ensures that the material fills every cavity of the mold.
- Cooling: Once the mold is filled, the material cools and solidifies. The cooling time varies depending on the material and the part’s thickness.
- Ejection: After cooling, the mold opens, and the finished part is ejected. This step requires precision to avoid damaging the part.
- Finishing: Additional processes like trimming, painting, or assembly may occur, depending on the final product requirements.
Factors Affecting Injection Molding Quality
Several factors can influence the quality of parts produced through polycarbonate and ABS injection molding:
- Material Quality: The quality of the resin directly impacts the final product. Using high-quality polycarbonate or ABS ensures better performance.
- Mold Design: A well-designed mold allows for better flow and cooling of the material, leading to higher-quality parts.
- Injection Speed: The speed at which the material is injected can affect the part’s finish and structural integrity.
- Temperature Control: Proper temperature settings during injection and cooling are crucial for achieving the desired properties in the final product.
Common Challenges in Injection Molding
While injection molding offers many benefits, it also comes with challenges. Some common issues include:
- Warpage: This occurs when parts cool unevenly, leading to distortion. Proper cooling and mold design can help mitigate this issue.
- Bubbles: Air trapped in the mold can create bubbles in the final product. Ensuring proper venting during the injection process can reduce this risk.
- Surface Defects: Imperfections on the surface can occur due to poor mold design or material issues. Regular maintenance and quality checks can help address these problems.
The Future of Injection Molding
As technology advances, the injection molding industry continues to evolve. Here are some trends shaping the future:
- Sustainability: There is a growing focus on using recycled materials and reducing waste in the injection molding process. This shift aligns with global sustainability goals.
- Automation: Automation in the injection molding process is increasing efficiency and reducing labor costs. Robotic systems can handle repetitive tasks, allowing for faster production times.
- 3D Printing Integration: The integration of 3D printing with injection molding is gaining traction. This combination allows for rapid prototyping and the production of complex geometries.
Conclusion
Polycarbonate and ABS injection molding are essential processes in modern manufacturing. Both materials offer unique benefits and applications. Understanding the differences and advantages of each can help manufacturers choose the right material for their needs.
Whether you’re producing automotive parts, consumer goods, or medical devices, knowing how to leverage these materials will enhance your production capabilities. As the industry continues to evolve, staying informed about trends and advancements will keep you ahead in the game.
For more information on polycarbonate injection molding, visit this link. To learn about ABS injection molding, check out this resource.