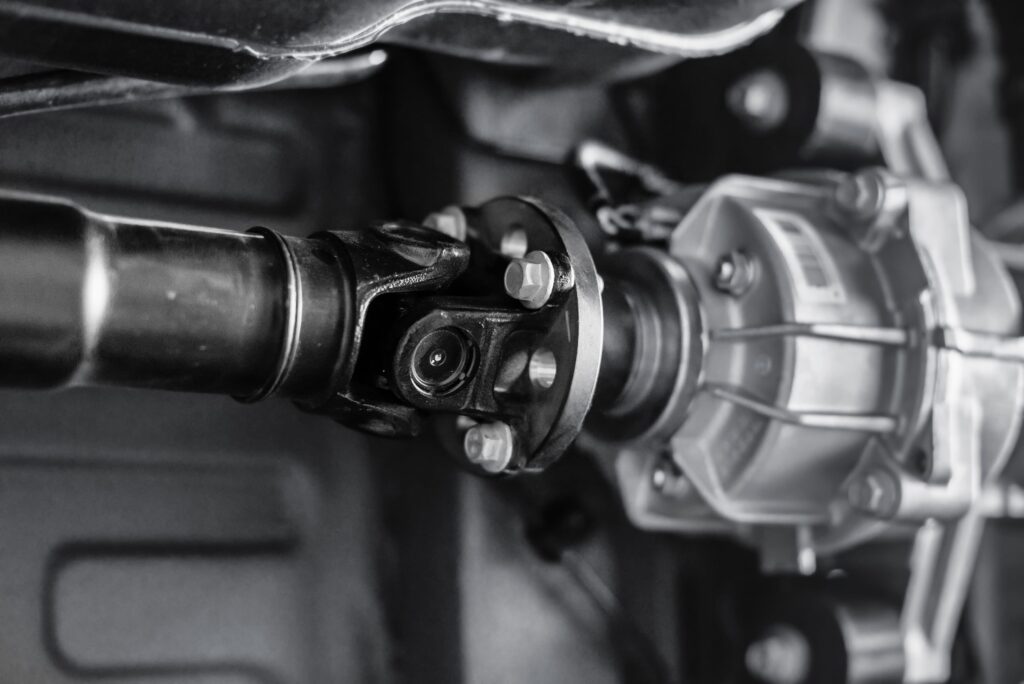
How Advanced Materials Are Enhancing Drive Shaft Performance
Drive shafts play a crucial role in power transmission across various industries, including automotive, aerospace, and industrial machinery. Traditionally manufactured using steel, drive shafts have evolved with the introduction of advanced materials that enhance performance, efficiency, and durability. The incorporation of these materials has led to significant improvements in strength-to-weight ratio, fuel efficiency, and overall operational reliability.
The Evolution of Drive Shaft Materials
Early drive shafts were predominantly made of solid steel due to its high strength and durability. However, steel’s density contributed to increased weight, limiting performance, especially in automotive and aerospace applications where weight reduction is critical.
The advent of aluminum alloys in drive shaft manufacturing provided a lightweight alternative while maintaining adequate strength. Aluminum drive shafts reduced vehicle weight, improving fuel efficiency and handling. However, they were still prone to deformation under extreme loads, necessitating further advancements in material technology.
According to a Drive Shaft Market report, the industry is expected to grow significantly in the coming years.
The Impact of Carbon Fiber Composites
One of the most revolutionary developments in drive shaft technology is the adoption of carbon fiber-reinforced composites. Carbon fiber drive shafts offer exceptional strength while being significantly lighter than their steel or aluminum counterparts. The benefits of carbon fiber drive shafts include:
- Reduced Weight: Carbon fiber is up to 60% lighter than steel, leading to lower rotational mass and improved energy efficiency.
- Higher Torque Transmission: Increased stiffness allows for efficient torque transfer with minimal power loss.
- Enhanced Durability: Carbon fiber is resistant to corrosion and fatigue, extending the lifespan of the drive shaft.
- Improved Vibration Damping: Reduced vibrations enhance vehicle stability and driver comfort.
Due to these advantages, carbon fiber drive shafts are increasingly used in high-performance vehicles, motorsports, and aerospace applications where weight and strength optimization are critical.
Titanium Alloys for High-Performance Applications
Titanium alloys have also emerged as a viable alternative for drive shafts, particularly in performance-driven applications. Titanium offers an excellent balance of strength, weight reduction, and corrosion resistance. Key benefits of titanium drive shafts include:
- Superior Strength-to-Weight Ratio: Titanium is lighter than steel but maintains comparable strength levels.
- Exceptional Corrosion Resistance: Ideal for use in harsh environments, including marine and aerospace applications.
- High Fatigue Resistance: Prolongs the life of the drive shaft under heavy load conditions.
Although titanium is more expensive than traditional materials, its benefits make it a preferred choice for high-performance and specialized applications.
Hybrid Drive Shafts: The Best of Both Worlds
To balance cost, performance, and durability, manufacturers are developing hybrid drive shafts that combine different materials. A common configuration involves using a steel or aluminum yoke with a carbon fiber shaft, optimizing both strength and weight. Hybrid drive shafts provide:
- Cost Efficiency: Reduced reliance on expensive materials while maintaining performance benefits.
- Enhanced Durability: Hybrid structures mitigate material-specific weaknesses, improving overall longevity.
- Customizable Performance: Manufacturers can tailor material combinations to specific application needs.
These hybrid designs are becoming popular in both commercial and high-performance vehicles, offering an optimal balance between performance and affordability.
The Future of Drive Shaft Materials
The future of drive shaft technology lies in continued advancements in material science. Emerging trends include:
- Nanomaterial Integration: The use of graphene and other nanomaterials to enhance strength and flexibility.
- Smart Materials: Self-healing composites that can repair micro-cracks, extending service life.
- 3D-Printed Drive Shafts: Additive manufacturing techniques for customized, lightweight, and high-strength drive shafts.
As industries demand higher efficiency and sustainability, the evolution of drive shaft materials will play a key role in shaping the next generation of power transmission systems.
Conclusion
Advanced materials such as carbon fiber composites, titanium alloys, and hybrid structures are revolutionizing drive shaft performance. These innovations offer superior strength, reduced weight, and enhanced durability, meeting the growing demands of automotive, aerospace, and industrial applications. With ongoing material research and technological advancements, drive shafts will continue to evolve, delivering improved efficiency, sustainability, and performance.