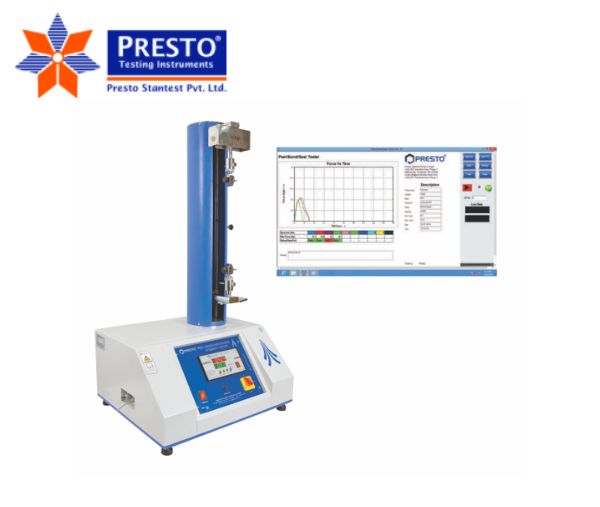
In the rapidly evolving world of packaging, flexible materials are becoming increasingly popular due to their lightweight nature, cost-effectiveness, and adaptability across various industries. However, the integrity of these packages depends largely on how well the layers of materials are bonded together.
This is where peel strength testing comes into play. The peel strength test in Bangladesh is gaining importance, especially as local manufacturers strive to meet global quality standards in packaging for food, pharmaceuticals, and consumer goods. By measuring the adhesive force required to separate two bonded layers, this test ensures that the packaging maintains its seal throughout transportation, storage, and usage.
Importance of Peel Strength in Flexible Packaging
Flexible packaging typically consists of multiple layers, such as films, foils, and adhesives that work together to protect the product inside. These layers must remain firmly bonded under different environmental and mechanical conditions. Peel strength is a direct measurement of the adhesive bond between these layers and indicates whether the package can endure normal handling without delaminating or leaking.
Peel strength testing becomes even more important when packaging needs to be resealable, tamper-evident, or heat-sealed. Poor bonding could result in torn packages, compromised seals, or even product recalls. In sectors like food or pharmaceuticals, such failures can have serious health and financial consequences.
Without proper adhesion, even the most visually appealing or technically advanced flexible package can fail, risking product contamination or spoilage. As the demand for reliable and export-grade packaging rises in Bangladesh, understanding the role of peel strength testing becomes essential. Therefore, ensuring the right level of peel strength is not only a technical requirement but also a critical factor in maintaining brand reputation and consumer safety.
Applications of Peel Strength Testing in Bangladesh
As Bangladesh strengthens its position in the global supply chain, especially in textiles, pharmaceuticals, and consumer goods, the need for high-performance packaging has increased. Peel strength testing is now being used widely across many sectors to assess the reliability of bonded materials.
Industries where peel strength testing is commonly applied include:
- Food packaging: Ensuring seals hold up during refrigeration, freezing, or transport.
- Pharmaceutical packaging: Maintaining sterility and preventing contamination.
- Textile labeling and lamination: Verifying label adhesion and laminated fabric durability.
- Industrial adhesives: Testing the bonding capability of various glues and tapes.
In each of these applications, a failure in bond strength can lead to significant product loss or safety issues. This makes routine testing a vital part of the quality control process.
How Peel Strength Testing Is Conducted
Peel strength testing involves placing a bonded sample in a tensile testing machine and pulling the two layers apart at a specific angle and speed. The force required to peel the layers is recorded and analyzed. These tests are generally performed at 90 or 180 degrees, depending on the product and application.
This method offers a standardized and repeatable way to compare different adhesive materials, coating processes, or manufacturing conditions. By identifying weak bonds early in production, manufacturers can make timely adjustments to improve adhesion quality and reduce rework or customer complaints.
Factors That Affect Peel Strength Results
While the test itself is straightforward, several factors can influence the outcome of a peel strength test. These variables must be controlled to ensure accuracy and consistency in results.
Some critical factors include:
- Surface treatment: Clean and properly treated surfaces bond better.
- Adhesive type: Different adhesives react differently under stress and temperature.
- Bonding pressure and temperature: Improper settings during lamination or sealing can weaken the bond.
- Environmental conditions: Humidity and heat can alter adhesive performance.
- Material thickness and flexibility: Thinner or softer materials may peel more easily, even with strong adhesion.
Understanding these variables allows for more precise control over the bonding process and helps improve packaging durability.
Why Demand is Rising for Peel Strength Testers in Bangladesh
With the increasing emphasis on export-quality goods and packaging compliance, there is a growing demand for reliable peel strength testers in Bangladesh. Manufacturers and quality control labs are investing in advanced testing equipment to maintain consistency in their products and meet the expectations of international buyers.
These machines not only provide accurate peel force measurements but also offer automation features, data logging, and compliance with ASTM or ISO testing standards. Having access to such tools enables local companies to compete more effectively in global markets by ensuring that their packaging performs as expected under real-world conditions.
Whether it’s testing new adhesives, checking packaging samples from suppliers, or validating internal quality processes, a peel strength tester is becoming an essential instrument in Bangladesh’s manufacturing and packaging sectors.