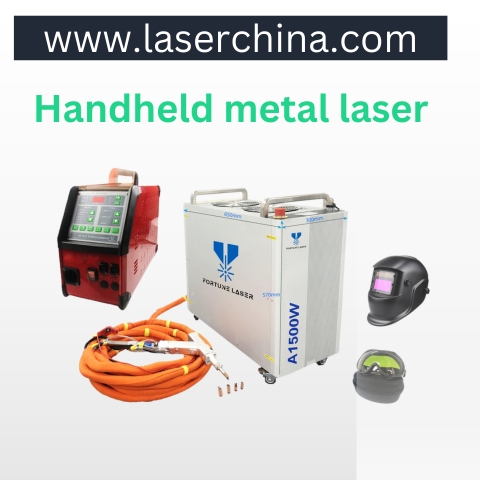
xr:d:DAF4QCUfMXM:16,j:6376384869998800468,t:23122809
The manufacturing industry in 2025 is undergoing a transformation, and at the heart of this change is the hand held metal laser. Once considered futuristic or niche, this compact yet powerful tool is now entering workshops, factories, and repair centers around the globe. But why is it steadily replacing traditional tools? The answer lies not in a single feature, but in a shift in how industries approach precision, productivity, and long-term reliability.
The Industrial Shift Towards Laser Technology
Industries have traditionally relied on mechanical methods for tasks like cutting, engraving, welding, and surface cleaning. These tools worked well in their time, but modern challenges require more accurate and efficient solutions. A hand held metal laser doesn’t just meet expectations—it redefines them. From automotive parts restoration to shipbuilding maintenance, businesses are looking for tools that can deliver consistent results with minimal downtime.
Today’s markets are competitive. Whether it’s small custom metal shops or large-scale fabrication plants, downtime, rework, and human error are unacceptable. This pressure has prompted businesses to seek tools that allow operators to work faster while still maintaining high standards of accuracy. That’s where the hand held metal laser steps in.
Real-Time Precision for Complex Jobs
Imagine needing to clean rust from a fragile machine part or engrave a serial number on a curved stainless steel surface. Traditional tools may struggle with such tasks, often leading to errors or surface damage. A hand held metal laser, by contrast, offers laser-guided precision, making it suitable for both detailed work and broader applications.
Its capacity to deliver uniform, consistent results, especially on intricate or hard-to-reach surfaces, makes it a reliable partner in demanding environments. It does not rely on physical contact, which eliminates vibration, reduces wear and tear, and improves accuracy.
On-Site Operation Without Setup Delays
Unlike large industrial machines that require pre-installation, calibration, or setup time, a hand held metal laser can be used directly on-site. This means maintenance teams can walk into a facility, bring out the unit, and get to work almost instantly. Whether it’s an offshore oil rig or a factory floor, mobility is a key advantage.
Portability opens up opportunities that previously required disassembling parts and transporting them to a workshop. With a hand held metal laser, much of this becomes unnecessary. The job gets done where the part is—no more interruptions in the production chain.
Durable Tools for Harsh Work Environments
Work environments can be harsh: dust, moisture, vibrations, and temperature extremes are common in industrial facilities. A hand held metal laser is engineered for such conditions. It’s enclosed in protective housing, often with active cooling, making it rugged enough for daily use. Unlike mechanical tools with multiple moving parts prone to wear, a laser-based system operates with optical components that are less likely to degrade over time.
The reduction in tool maintenance alone is a powerful motivator for businesses. Every hour a tool is down for repair is an hour of lost productivity. With the stability of a hand held metal laser, companies avoid this problem altogether.
Flexibility in Application
One of the most underrated strengths of a hand held metal laser is its flexibility. It’s not just a tool for one task—it’s a platform for multiple functions. Operators can switch between cleaning, marking, engraving, and surface preparation, depending on the specific model and configuration.
Take metal cleaning, for example. Removing oxidation, oil, or contaminants from metal surfaces often requires chemical solvents or abrasive blasting—both of which are labor-intensive and environmentally hazardous. A hand held metal laser does it faster, without chemicals, and without damage to the base material.
Switch to marking, and the same unit can etch permanent identification codes, barcodes, or logos onto metal parts with millimeter precision. It becomes a traceability tool, a quality control asset, and a compliance enabler all in one.
Reduced Operating Costs
Every manufacturing manager considers not just the purchase price of a tool but its total cost of ownership. Mechanical tools come with recurring costs—blades, fluids, replacements, service visits. A hand held metal laser dramatically reduces these overheads. Since there’s no physical contact, there’s no blade to dull, no oil to change, and no brushes to replace.
In addition, many units come with intuitive controls and require minimal training, reducing labor costs and improving operator adoption. Skilled technicians are in short supply, and any tool that shortens the learning curve is a win for operational efficiency.
Regulatory Compliance and Clean Workflows
As industrial safety and environmental regulations grow stricter, traditional cleaning or marking methods are becoming liabilities. Chemical-based cleaning leaves behind waste. Sandblasting creates dust. Even mechanical engraving can generate particles or noise pollution.
A hand held metal laser avoids all of this. There’s no dust cloud, no fluid runoff, and no post-processing mess to clean. This not only reduces health risks for operators but also helps facilities comply with local and international standards.
Moreover, as sustainability becomes a focus area for manufacturers, using tools that align with greener practices can give a business a competitive edge. When procurement departments compare vendors, the use of eco-conscious tools like a hand held metal laser often tips the scales.
Adapting to Future Needs
Industries are evolving. The parts, materials, and tolerances of today may look very different in five years. What doesn’t change is the need for adaptable tools. A hand held metal laser fits into this narrative. It works on various metals—stainless steel, aluminum, copper, brass—without changing heads or consumables.
Manufacturers investing in these tools are preparing for flexible production. Whether they shift to aerospace-grade materials or high-precision medical components, the same laser tool can keep up.
Integration with Digital Systems
In an era of smart factories and digital monitoring, tools must be more than mechanical performers—they need to be part of a connected system. Advanced hand held metal laser models can be integrated into workflow management software, provide operational data, and even offer remote diagnostics.
Such integration ensures process visibility, helping managers track productivity and spot irregularities early. In lean manufacturing environments, this data becomes critical for continuous improvement.
Global Availability and Service Network
One reason behind the rising popularity of the hand held metal laser is improved global distribution. Manufacturers from Germany, China, the U.S., and Japan have created extensive networks for supply and after-sales service. Businesses, whether in Europe, Asia, or the Middle East, now have access to affordable units and localized support.
Unlike earlier years when service delays affected adoption, today’s users benefit from responsive technical support, operator training, and spare parts delivery—all of which make the laser tool a safer investment.
Final Thoughts
The transition toward hand held metal laser tools isn’t a passing trend—it’s a strategic move driven by industrial needs. In a world where efficiency, precision, sustainability, and compliance are non-negotiable, traditional methods can no longer deliver. The hand held metal laser meets these demands head-on, making it more than a tool—it’s an essential part of the modern industrial toolkit.
From fabrication floors to maintenance crews, decision-makers are recognizing its value. It’s not about replacing old methods for the sake of innovation. It’s about choosing a tool that keeps businesses competitive, efficient, and future-ready.